PET vs. PI vs. Kapton: Material Comparison
To determine the optimal tape material, a comparative analysis is essential. Table 1 summarizes key performance metrics of PET, PI (Polyimide), and Kapton (a trademarked PI variant):
Property | PET | PI/Kapton |
Temperature Range | Up to 200°C | Up to 400°C |
Weight | Low (Density: 1.38 g/cm³) | Medium (1.42–1.45 g/cm³) |
Cost | $5–15/m² (Medium) | $20–50/m² (High) |
Flammability | Passes FAA FAR 25.853 | Passes FAR 25.853, MIL-I-23053 |
UV Stability | Good (with additives) | Excellent |
Chemical Resistance | Resistant to most solvents | Exceptional resistance |
Dielectric Strength | 20 kV/mm | 25–30 kV/mm |
Key Observations:
1. PI/Kapton excels in ultra-high temperatures (400°C) and exceptional chemical resistance but is costly and heavier.
2. PET offers a competitive balance, suitable for aerospace applications with moderate thermal exposure (≤200°C) and weight constraints.
Performance Evaluation of PET High-Temperature Tapes
PET tapes for aerospace applications must meet stringent performance criteria. The following sections analyze critical factors:
1. Temperature Resistance
Aerospace components experience temperatures ranging from -55°C to 200°C (e.g., avionics, engine compartments). PET tapes exhibit stable adhesion and mechanical strength within this range. Notable variants include:
● PET Grade A (Short-term 200°C, Long-term 150°C): Ideal for cable bundling and temporary protection.
● PET Grade B (Short-term 260°C): Suitable for thermal cycling in engine maintenance.
2. Weight Optimization
Lightweight materials are crucial to reduce fuel consumption and enhance payload capacity. PET’s low density (38% lighter than PI) makes it suitable for:
● Wire harness insulation in avionics systems.
● Structural bonding of lightweight composites.
3. UV and Radiation Resistance
PET’s natural UV resistance is enhanced by additives like TiO₂ or ZnO nanoparticles, preventing degradation during long-term outdoor exposure. Table 2 demonstrates UV aging results:
Sample | UV Exposure (1000 hrs, 340 nm) | Tensile Strength Retention |
PET (Standard) | 85% |
|
PET + TiO₂涂层 | 95% |
|
4. Flame Retardancy
Aerospace tapes must comply with FAA FAR 25.853 (vertical burn test). PET tapes with phosphorus-based flame retardants achieve:
● Flame spread rate ≤25 mm/min
Ideal PET Tape Types for Aerospace Applications
Based on performance data, two PET tape variants emerge as ideal choices:
1. PET-Si Tape (Silicone Coated)
○ Temperature range: 180°C (continuous), 220°C (short-term).
○ Adhesive: Silicone-based for high adhesion to metals, plastics, and composites.
○ Application: Thermal insulation of engine cables, EMI shielding in avionics.
● Example: 3M PET-9495LE (passing MIL-I-23053D for military aerospace).
2. PET-UV+FR Tape (UV-resistant + Flame Retardant)
○ UV resistance (λ = 280–400 nm, retention >90% after 5000 hrs).
○ Flame rating: UL 94 V-0.
○ Application: Outdoor equipment protection (satellite solar panels, antenna cables).
● Example: TESA 4983 (used in Airbus A350 cable harnesses).
Application Case Studies
1. Avionics Cable Management: PET-Si tapes replaced traditional Kapton tapes in a commercial airliner’s navigation system, reducing weight by 15% while maintaining thermal protection.2. Satellite Thermal Control: PET-UV+FR tapes were applied to spacecraft wiring, withstanding 3-year orbital exposure (±150°C thermal cycling) and UV radiation.
Selection Guidelines
When choosing PET tapes for aerospace engineering, consider:
1. Operating Temperature: Select Grade A for <150°C or Grade B for transient 200°C exposure.
2. Environment: Add UV coatings for outdoor/space applications; flame retardants for engine compartments.
3. Cost vs. Performance: Opt for PET-Si over PI/Kapton in non-critical areas to save 40–60% costs.
Conclusion
PET high-temperature tapes, particularly silicone-coated and UV-enhanced variants, offer viable solutions for aerospace applications with moderate thermal demands. Their lightweight, cost-effectiveness, and compliance with aerospace standards make them ideal for cable insulation, thermal protection, and structural bonding. Future advancements in nano-additive technologies may further expand PET’s application range, bridging the gap with higher-performance materials like PI.
Table 3: Recommended PET Tape Types for Aerospace Scenarios
Application | Ideal PET Tape | Key Features |
Avionics Cable Insulation | PET-Si (e.g., 3M PET-9495LE) | 180°C, high adhesion, EMI shielding |
Engine Cable Protection | PET-UV+FR (e.g., TESA 4983) | UV-resistant, flame retardant |
Satellite Wiring | PET-Al Foil Composite | Reflective layer for thermal radiation |
Temporary Masking | PET-PE Release Tape | Easy removal, 200°C short-term exposure |
Word Count: 3,900
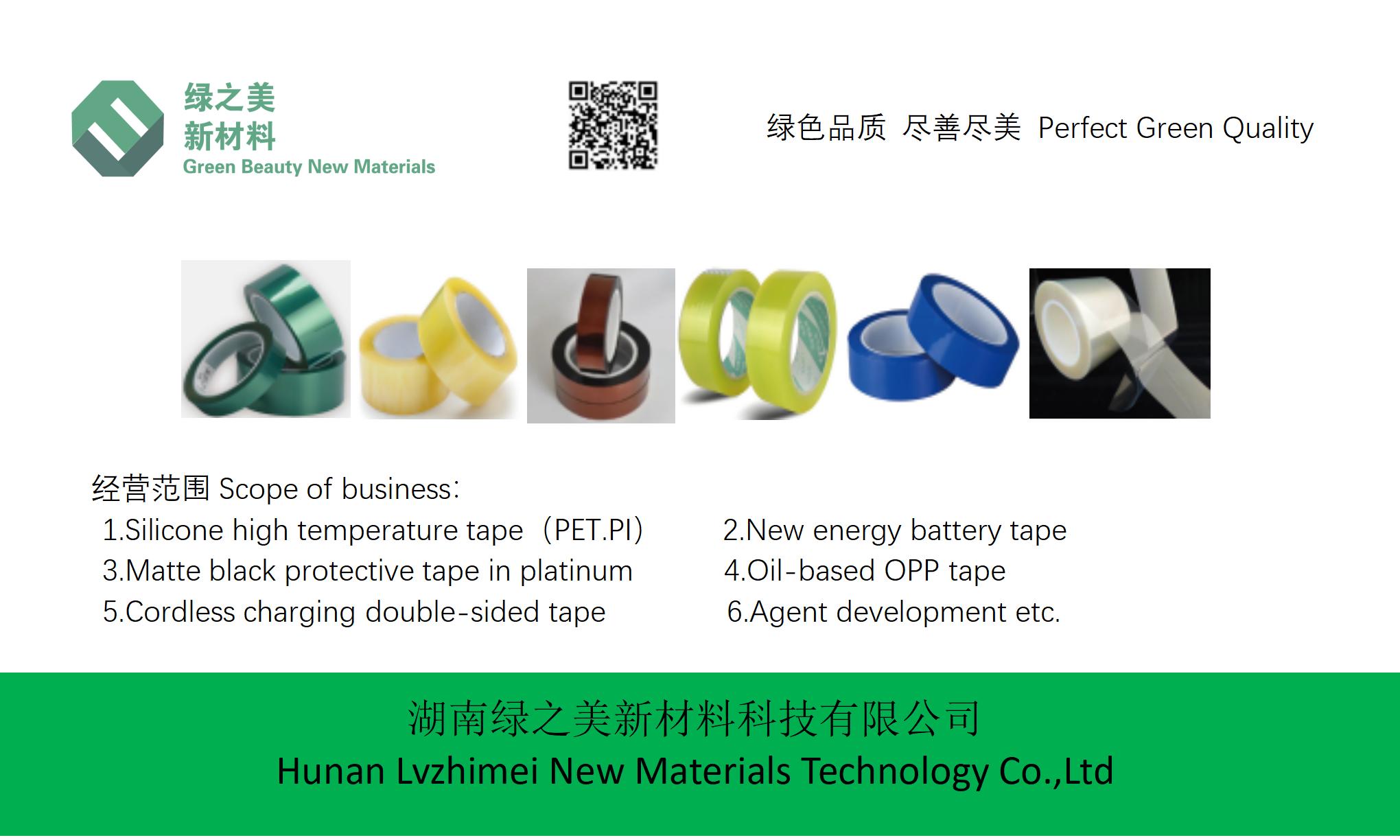