IntroductionSelf-adhesive back blocking spray paint tape plays a vital role in protecting surfaces during painting processes, ensuring precision and preventing contamination. In industries like automotive and aerospace, where stringent quality and safety standards are imperative, understanding the regulatory requirements for such tapes is essential. This article delves into the safety standards, highlighting key performance criteria and comparative evaluations with other high-temperature tapes, particularly PET and brown circuit board variants.
1. Safety Standards for Self-Adhesive Back Blocking Spray Paint TapeSafety standards for this tape are governed by multiple regulatory bodies and industry-specific norms. Key aspects include:
1.1 Material Composition
● Adhesive Properties: The tape must use high-grade pressure-sensitive adhesives (PSA) that adhere firmly to substrates without leaving residue upon removal. Commonly, acrylic-based adhesives are preferred for their stability at high temperatures.
● Backing Material: The tape’s backing layer is typically made of polyimide (Kapton) or PET film. Polyimide offers superior resistance to thermal stress (up to 260°C), while PET is suitable for lower temperature ranges (up to 150°C). Safety standards demand material purity to prevent chemical leaching.
1.2 Temperature Resistance
● Automotive applications require tapes to withstand temperatures up to 200°C during curing processes (e.g., oven baking). Aerospace standards may demand higher resistance (250°C or more) for prolonged exposure in engine compartments.
● Certifications like ASTM D648 and ISO 22007-2 specify thermal stability testing methods, ensuring the tape does not deform, delaminate, or release harmful fumes.
1.3 Chemical Resistance
● Resistance to solvents, paints, and cleaning agents is crucial. Tapes must withstand exposure to chemicals like xylene, acetone, and methylethylketone (MEK) without degradation. Automotive standards (e.g., GMW3059) outline solvent immersion tests.
● Aerospace industry compliance (e.g., AS9100) mandates resistance to aviation fuels, lubricants, and hydraulic fluids to prevent tape failure in critical environments.
1.4 Adhesion and Peel Strength
● Standards define minimum peel strength values (e.g., ASTM D3330) to ensure the tape remains intact during application and removal. Automotive manufacturers often require ≥10 N/cm peel strength to avoid adhesive transfer to painted surfaces.
2. Comparison with Adhesive PET Material High-Temperature TapePET tapes, while cost-effective, differ significantly in performance:
Parameter | Self-Adhesive Back Blocking Tape | PET High-Temp Tape |
Max Temperature Resistance | Up to 260°C (Polyimide backing) | Up to 150°C |
Chemical Resistance | High (Resistant to MEK, xylene) | Moderate (Limited MEK) |
Certification | ASTM D3330, ISO 9001 | ASTM D3421 |
Application | Automotive/aerospace paint masking | Electronics assembly |
Cost | Higher | Lower |
Key Observations:
● PET tapes are suitable for electronics manufacturing but may fail in automotive curing ovens. Their chemical resistance is insufficient for aerospace applications.
3. Comparison with Brown Circuit Board High-Temperature TapeBrown tapes (commonly polyimide-based) share similarities but target different applications:
Parameter | Self-Adhesive Back Blocking Tape | Brown Circuit Board Tape |
Adhesive Type | PSA (permanent/removable) | PSA (permanent) |
Temperature Range | 200-260°C | Up to 300°C |
Purpose | Paint masking | Circuit board protection |
Chemical Resistance | Solvents, lubricants | Acid/alkali resistance |
Certifications | GMW3059, AS9100 | IPC-TM-650 |
Flexibility | High (conforms to curved surfaces) | Moderate |
Key Observations:
● Brown tapes excel in electronics soldering processes but lack the peel strength and flexibility required for automotive paint masking.
4. Chemical Resistance CertificationsKey certifications for these tapes include:
○ GMW3059 (General Motors): 168-hour solvent resistance test.
○ PV 3900 (Volkswagen): Evaluates tape behavior under thermal cycling and chemical exposure.
○ AS9100D (IAQG): Quality management system standard, indirectly influencing material requirements.
○ AMS-DTL-23053 (SAE): Defines high-temperature tape properties for aerospace applications.
○ IPC-TM-650: Method 2.4.8 assesses tape resistance to soldering fluxes and thermal shock.
5. Application-Specific ComplianceAutomotive Industry:
Tapes must meet Tier 1 supplier requirements, ensuring consistency across production lines. Audits by regulatory bodies like IATF 16949 verify adherence to peel strength, temperature, and chemical resistance tests.
Aerospace Industry:
Compliance with FAA/EASA directives demands traceability of tape materials. Each batch must provide certification data, including thermal aging tests (per ASTM E1593) to predict long-term performance in extreme environments.
6. Challenges and Future Trends
● Environmental Concerns: Shift towards low-VOC (volatile organic compound) adhesives to meet EPA/REACH regulations.
● Advanced Testing: Integration of AI-driven systems to monitor tape performance during manufacturing processes.
● Nano-Technology: Development of tapes with self-healing adhesives to enhance durability.
ConclusionSelf-adhesive back blocking spray paint tape must adhere to stringent safety standards, balancing temperature resistance, chemical robustness, and peel strength. While PET and brown circuit board tapes offer niche applications, back blocking tapes excel in automotive and aerospace paint masking due to their specialized certifications. Future advancements will focus on eco-friendly formulations and digital verification systems to ensure continuous compliance. Understanding these standards is pivotal for industries seeking reliable, high-performance materials.
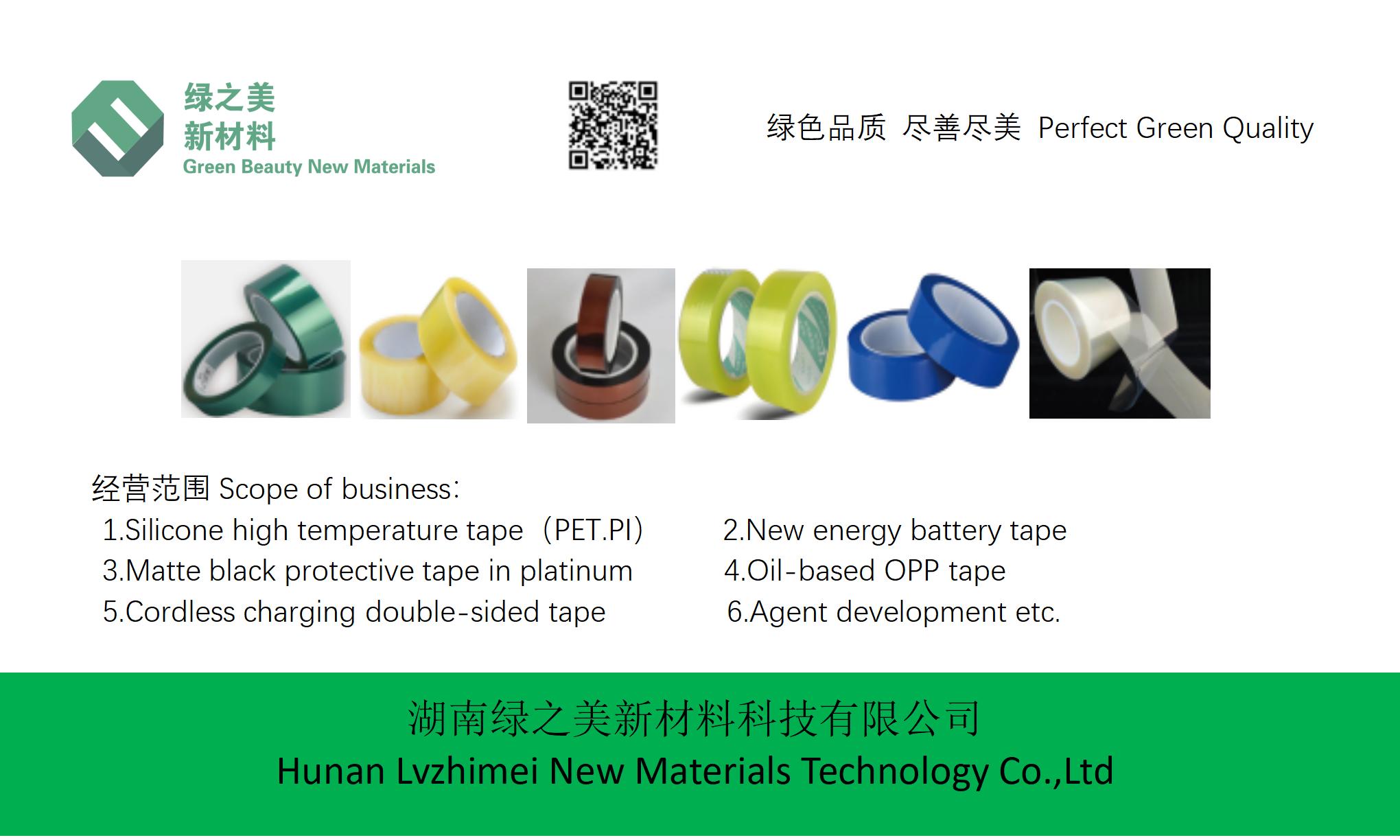