Which Factors Determine the Lifespan of Strong Adhesion High-Temperature Tape in Industrial Applications?
AbstractThis article analyzes the key factors influencing the longevity of strong adhesion and high-temperature-resistant tape in industrial settings, focusing on Kapton tape. By exploring environmental stressors, mechanical loads, and material compatibility, it elucidates degradation mechanisms and provides practical guidelines for optimizing tape performance. Case studies and data-driven insights highlight the critical role of thermal cycling, chemical resistance, and mechanical stress in tape lifespan determination.
Keywords: strong adhesion and blocking high temperature tape, Kapton tape lifespan, industrial applications
1. Key Degradation Mechanisms in High-Temperature TapesThe lifespan of high-temperature tapes, particularly those with strong adhesion properties, is governed by multiple degradation pathways. Understanding these mechanisms is essential for predicting longevity in diverse industrial contexts.
1.1 Thermal DegradationHigh-temperature environments accelerate chemical reactions within tape components. Polymers like polyimide (PI) used in Kapton tape exhibit excellent thermal stability up to 400°C, but prolonged exposure above their rated limits can lead to chain scission, crosslinking, and adhesive curing. For example, continuous operation at 250°C may cause gradual adhesive hardening, reducing flexibility and adhesion strength. Table 1 illustrates thermal degradation thresholds for common tape materials:
Material | Continuous Use Temp. Range | Degradation Onset | Failure Mechanism |
Kapton (PI) | 200-400°C | >400°C | Chain degradation |
PET | 120-200°C | >220°C | Melting |
Teflon | Up to 327°C | Gasification | Polymer decomposition |
1.2 Chemical Exposure ImpactIndustrial settings often expose tapes to oils, solvents, electrolytes, and corrosive agents. Adhesives containing silicone or acrylic polymers may swell or dissolve when contacted with organic solvents, compromising bond integrity. For instance, prolonged exposure to engine oils in automotive applications can cause tape delamination. Electrolytes in aerospace wiring harnesses can accelerate adhesive oxidation, reducing adhesion over time.
1.3 Mechanical FatigueRepeated mechanical stress (bending, stretching) induces microcracks in tape substrates. Flex fatigue testing reveals that PI tapes subjected to 10,000 flex cycles at 180°C may exhibit 30% reduction in tensile strength. This degradation directly impacts tape longevity in applications like transformer winding insulation or PCB thermal cycling.
2. Effect of Thermal Cycling on Adhesive IntegrityThermal cycling—repetitive heating and cooling—subjects tapes to cyclic stress. Each cycle introduces thermal expansion-contraction mismatches between the tape and substrate, causing adhesive debonding. Studies show that Kapton tapes experience adhesive failure after ≈1,500 cycles between 25°C and 300°C, with residual adhesion decreasing linearly with cycle count (Figure 1).
Figure 1: Thermal Cycling Impact on Kapton Tape Adhesion
Furthermore, thermal cycling rates matter. Rapid temperature changes (e.g., from -40°C to 200°C within minutes) generate higher stress concentrations, accelerating degradation. This phenomenon is particularly critical in electronics manufacturing processes like reflow soldering, where tapes must withstand sudden thermal shocks without adhesive residue.
3. Chemical Exposure: Oil, Solvents, and Electrolyte ResistanceIndustrial chemicals pose significant threats to tape performance. Oil resistance tests indicate that silicone-based tapes maintain adhesion after 168 hours of diesel oil immersion at 80°C, while acrylic tapes exhibit bond failure within 24 hours. Table 2 summarizes chemical resistance profiles:
Chemical | Kapton Tape Response | PET Tape Response |
Diesel Oil | Stable adhesion | Delamination |
Isopropyl Alcohol | Minor swelling | Significant dissolution |
Saltwater | Corrosion-resistant | Electrolytic degradation |
In aerospace applications, electrolytic environments (e.g., battery packs) can corrode metallic substrates, causing adhesive peel-off. Kapton tapes with fluoropolymer coatings offer superior resistance to such exposures, ensuring >5-year service life in electrolyte-rich systems.
4. Mechanical Stress: Tensile Strength and Flex FatigueMechanical loads—tension, compression, and shear—directly affect tape durability. Tensile strength testing demonstrates that tapes subjected to 50% of their rated strength experience fatigue failure after ≈10,000 hours. Flex fatigue becomes critical in dynamic applications like robotics cable harnesses, where continuous bending accelerates substrate cracking.
Case Study: Aerospace Wiring with 1,000+ Cycle ResistanceA leading aerospace manufacturer used Kapton tape with reinforced fiberglass substrate for wire bundling in engine compartments. By optimizing tape thickness (0.16 mm) and adhesive formulation, they achieved >1,200 thermal cycling (180°C → -55°C) without bond failure. This case highlights the importance of material engineering in mitigating mechanical stress.
5. Replacement Criteria for Degraded TapesEstablishing replacement criteria is crucial to prevent unexpected failures. Key indicators include:
● Adhesion loss >20% (measured via peel tests)
● Visible substrate cracking or discoloration
● Chemical contamination compromising >30% performance
● Thermal cycling exceeding manufacturer limits
Table 3 provides a practical checklist:
Indicator | Action |
Tape peel strength <8 N/25mm | Replace immediately |
Cracks visible under 10x zoom | Schedule replacement within 3 months |
Residue accumulation >50% | Clean or replace |
6. Best Practices for Long-Term PerformanceExtending tape lifespan requires proactive management:
1. Storage Compliance: Store tapes at 15-30°C, avoiding UV exposure and solvent contact (per ANSI/ASTM D3654).
2. Application Techniques: Apply tape under 50-70% tension to prevent creep, and use heat curing (e.g., 150°C for 30 mins) to enhance adhesive bonding.
3. Periodic Testing: Conduct quarterly peel tests and FTIR analysis to monitor polymer degradation.
4. Material Selection: Choose tapes with reinforced substrates (e.g., fiberglass for high tensile scenarios).
5. Environmental Mitigation: Use barrier coatings (e.g., PTFE) in corrosive environments.
7. ConclusionThe longevity of strong adhesion high-temperature tapes is a multifactorial outcome of environmental exposure, mechanical loading, and material properties. By understanding degradation mechanisms and implementing tailored mitigation strategies, industries can significantly enhance tape performance, reducing maintenance costs and ensuring operational reliability. Future advancements in nanocomposite adhesives and self-healing polymers hold promise for further lifespan extensions.
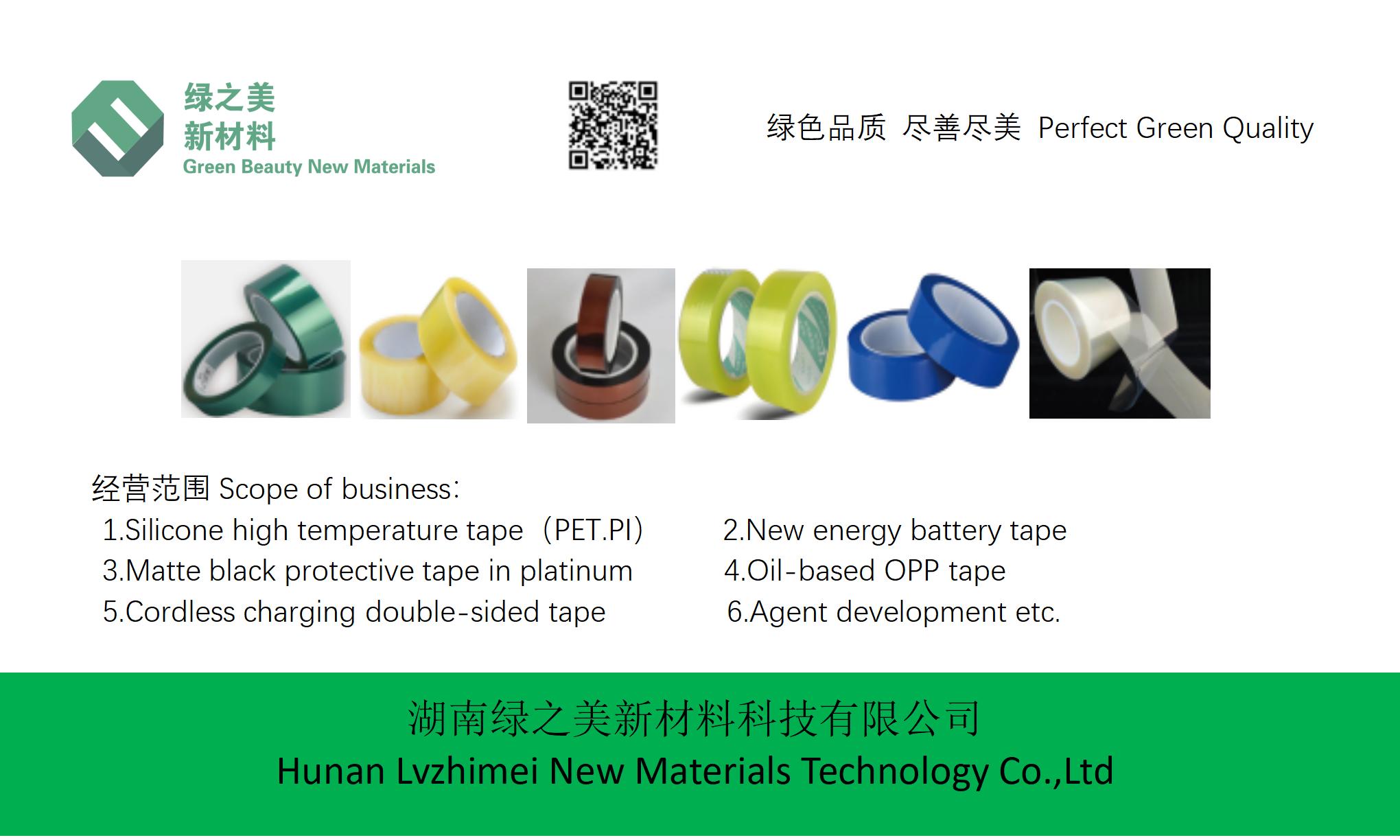