What Makes Brown Circuit Board High Temperature Tape Unique?
IntroductionIn the intricate world of electronics manufacturing, precision and durability are non-negotiable requirements. Circuit board high temperature tapes play a pivotal role in ensuring the reliability and longevity of printed circuit boards (PCBs) during production and operation. Among these tapes, brown circuit board high temperature tape stands out for its unique properties and widespread adoption in various industries. This article delves into the advantages of brown polyimide tape, focusing on its color significance, heat resistance properties, and industry applications, shedding light on why it is a preferred choice for PCB masking and insulation.
1. Color Significance in PCB MaskingThe color of high temperature tape is not merely aesthetic; it serves functional purposes in the PCB manufacturing process. Brown circuit board tape is specifically designed to meet the demands of modern electronics production, where visual differentiation and process efficiency are critical. The brown hue offers several advantages:
1.1 Visual Contrast for Precision WorkIn PCB assembly lines, technicians handle minute components and intricate circuitry. Brown tape provides excellent contrast against the typical green solder mask layer found on most circuit boards. This color differentiation enhances visibility during manual operations, such as component placement, soldering, and inspection. By reducing eye strain and improving focus, brown tape helps minimize errors and improve production efficiency.
1.2 UV Light Blocking PropertiesDuring certain PCB manufacturing stages, ultraviolet (UV) curing processes are employed to solidify solder masks or adhesives. Brown tape acts as an effective barrier against UV light, preventing unintended curing or degradation of underlying materials. Its opacity ensures that only designated areas are exposed to UV radiation, maintaining process consistency and product quality.
1.3 Identification and TraceabilityIn complex electronic assemblies, different colored tapes can indicate specific functions or zones. Brown tape is often used to mark areas requiring high-temperature resistance, such as SMT (surface mount technology) component zones or regions subjected to thermal cycling during testing. This color coding aids in quality control and facilitates troubleshooting by quickly identifying critical sections of the board.
Table 1: Comparative Color Analysis in PCB Masking
Tape Color | Key Advantages | Typical Applications |
Brown | UV blocking, high contrast, | SMT zones, thermal management areas, |
heat resistance | rework masking |
|
Green | Standard solder mask compatibility | General circuit protection |
Yellow | Temporary marking, low-temp | Component identification, temporary fix |
White | High visibility for small parts | Debugging, test point marking |
Black | EMI shielding, heat absorption | Heat sinks, EMI-sensitive regions |
2. Heat Resistance PropertiesThe core strength of brown circuit board high temperature tape lies in its exceptional thermal performance. Composed primarily of polyimide films (e.g., Kapton) and advanced adhesive systems, it exhibits properties that surpass traditional insulation materials:
2.1 Temperature Range and StabilityBrown tapes are engineered to withstand extreme temperatures, with typical operating ranges from -70°C to +260°C. This wide thermal tolerance ensures performance stability during processes like reflow soldering (up to 260°C), wave soldering, and prolonged exposure to high-temperature environments. Unlike standard PVC or PET tapes that may deform or delaminate under heat, brown polyimide tape maintains its structural integrity, preventing component displacement or insulation failure.
2.2 Chemical and Corrosion ResistancePCB manufacturing involves exposure to solvents, fluxes, and other chemicals. Brown tape’s polyimide base exhibits superior resistance to corrosive agents, ensuring it remains functional even in harsh environments. Additionally, its non-adhesive residue characteristic means that after removal (e.g., post-soldering), no sticky residues are left behind, avoiding contamination of delicate circuitry.
2.3 Mechanical Strength and FlexibilityThe tape’s construction combines mechanical robustness with flexibility. It can withstand mechanical stress during handling, assembly, and thermal cycling without tearing or cracking. This durability is particularly crucial in applications where components undergo repeated thermal expansion and contraction, such as automotive electronics or industrial control systems.
2.4 Electrical Insulation PerformanceElectrical insulation is a paramount concern in PCBs. Brown tape offers high dielectric strength (up to 3,000 V/mil) and low electrical conductivity, preventing short circuits and arcing. Its stable insulation properties across temperature extremes ensure consistent performance even in environments with fluctuating thermal conditions.
Table 2: Key Technical Specifications of Brown Polyimide Tape
Property | Value/Range |
Thickness | 0.05mm – 0.25mm |
Adhesion Strength | 10-30 N/25mm |
Tensile Strength | 150-300 N/cm |
Dielectric Breakdown | >3,000 V/mil |
Max Operating Temp. | -70°C to +260°C |
Chemical Resistance | Solvents, acids, alkalis |
3. Industry Adoption and ApplicationsThe versatility and reliability of brown circuit board high temperature tape have driven its adoption across diverse sectors. Key industries leveraging its advantages include:
3.1 Electronics ManufacturingIn the production of consumer electronics (smartphones, laptops), industrial control systems, and telecommunications equipment, brown tape is indispensable. It is used for:
● Masking during soldering to protect sensitive areas from heat and solder bridging.
● Insulating traces and components in high-density PCBs.
● Temporary bonding of components during assembly to prevent movement.
3.2 Automotive ElectronicsThe stringent requirements of automotive environments—high engine temperatures, vibration, and exposure to fluids—demand durable materials. Brown tape finds applications in:
● Engine control units (ECUs) for thermal and vibration protection.
● Wiring harness insulation in hybrid/electric vehicles.
● Sensor and module protection in underhood electronics.
3.3 Aerospace and DefenseIn aerospace applications where weight reduction and reliability are critical, brown tape’s lightweight yet robust properties are ideal. It is used for:
● Insulating avionics systems exposed to extreme temperatures.
● Masking during conformal coating processes.
● Protecting military electronics from environmental hazards.
3.4 Solar and LED TechnologyThe high-temperature resistance and UV stability of brown tape make it suitable for solar panel and LED module manufacturing. It aids in:
● Sealing junction boxes to prevent moisture ingress.
● Insulating interconnects in solar cells subjected to prolonged sunlight exposure.
● Masking during thermal curing of LED encapsulants.
3.5 Research and LaboratoriesIn R&D settings where prototypes undergo rigorous testing, brown tape’s flexibility and reusability are valued. It facilitates:
● Temporary modifications and repairs without damaging boards.
● Thermal protection during accelerated aging tests.
● Custom masking for specialized experiments.
4. Advantages Over Alternative MaterialsBrown polyimide tape distinguishes itself from competitors through a combination of properties:
4.1 Comparison with PET and Silicone Tapes
● PET Tape: While cost-effective, PET tapes have lower temperature limits (typically <150°C) and inferior chemical resistance. Brown polyimide tape offers superior performance in high-stress environments.
● Silicone Tape: Though silicone tapes are heat-resistant, they often exhibit lower mechanical strength and higher costs. Brown polyimide tape balances durability and affordability.
4.2 Long-Term ReliabilityIts resistance to thermal aging and degradation ensures consistent performance over the lifespan of electronic devices, reducing maintenance costs and warranty claims.
4.3 Process EfficiencyThe tape’s ease of application and removal, combined with its non-residue property, streamlines manufacturing processes and minimizes post-processing cleanup.
5. Future Trends and InnovationsAs electronics evolve toward miniaturization and higher power densities, the demand for advanced high-temperature tapes is growing. Future developments in brown tape technology may focus on:
● Enhanced thermal conductivity for heat dissipation management.
● Integration with smart materials for real-time temperature monitoring.
● Bio-based or recyclable formulations to meet sustainability goals.
ConclusionBrown circuit board high temperature tape’s uniqueness lies in its synergistic blend of thermal resilience, mechanical strength, electrical insulation, and functional coloration. From safeguarding PCBs during soldering to enabling reliable performance in extreme environments, its advantages have solidified its status as a cornerstone material in modern electronics manufacturing. As industries continue to push the boundaries of technology, brown polyimide tape will remain a vital tool, evolving to meet emerging challenges and drive innovation forward.
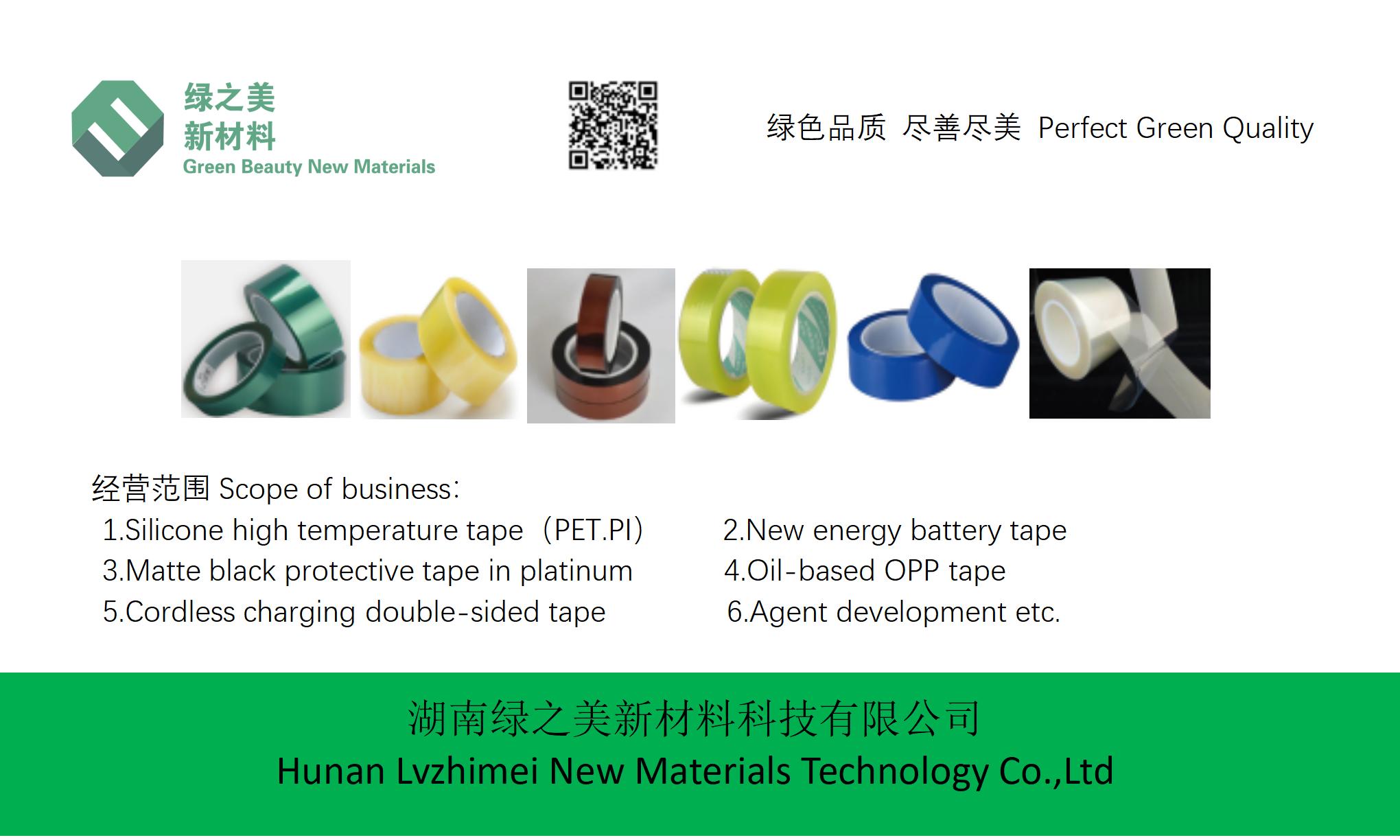