How Does Polyimide Tape Work in High-Temperature Environments?
Article 2: How Does Polyimide Tape Work in High-Temperature Environments?https://www.lvmeikapton.com
Abstract:This article delves into the mechanisms behind the exceptional performance of polyimide tape (PI tape) in high-temperature environments. Focusing on its molecular structure, adhesive properties, and thermal stability, the analysis demonstrates how PI tape withstands extreme heat while maintaining strong adhesion, electrical insulation, and chemical resistance. Case studies and performance metrics highlight its applications in automotive, electronics, and industrial processes, emphasizing its role as a critical material in high-temperature protection.
Keywords: Polyimide tape, high-temperature resistance, adhesive PET material, thermal stability, lvmeikapton, molecular structure, automotive spray paint protection.
Table of Contents
2. The Science Behind Polyimide Tape
2.1 Molecular Structure of Polyimide
2.2 Thermal Stability Mechanisms
3. Performance Metrics and Technical Specifications
3.1 Temperature Resistance Range
3.2 Adhesion and Shear Strength
3.3 Electrical Insulation Properties
4. Adhesive Systems: Key to High-Temperature Performance
4.1 Silicone-Based Adhesives
4.2 Other Adhesive Types (Acrylic, Rubber)
5. Case Study: Automotive Industry Application
5.1 Self-Adhesive Back Blocking Spray Paint Tape
5.2 Performance in Extreme Conditions
6. Applications in Electronics and Industrial Settings
6.1 Wave Soldering Protection in PCBs
6.2 Motor and Transformer Insulation
6.3 Chemical and Radiation Resistance
7. Comparative Analysis: PI Tape vs. Alternative Materials
8. Future Developments and Innovations
1. IntroductionPolyimide tape, also known as Kapton tape or PI tape, is a versatile material renowned for its ability to withstand extreme temperatures, maintain robust adhesion, and exhibit exceptional electrical and chemical resistance. Composed of a polyimide film substrate coated with specialized adhesives, this tape plays a crucial role in protecting components subjected to high-temperature processes, such as wave soldering, thermal curing, and automotive涂装. This article aims to elucidate the scientific principles and engineering features that empower PI tape to function effectively in environments exceeding 300°C.
2. The Science Behind Polyimide Tape2.1 Molecular Structure of PolyimidePolyimide (PI) is a class of polymers characterized by the presence of imide rings (-CO-NR-CO-) in their main chain. The molecular structure is primarily derived from the reaction of aromatic diamines (e.g., 4,4'-diaminodiphenyl ether) and aromatic dianhydrides (e.g., pyromellitic dianhydride). The resulting polymer exhibits a rigid, planar backbone due to the aromatic rings and strong intermolecular forces provided by the polar imide bonds. This structure imparts several key properties:
● Thermal Stability: The aromatic rings and imide bonds offer high bond energies, resisting thermal degradation up to 500°C.
● Mechanical Strength: The tightly packed molecular chains enhance tensile strength and dimensional stability.
● Chemical Resistance: The non-reactive nature of the polymer enables resistance to acids, solvents, and radiation.
2.2 Thermal Stability MechanismsPI tape's resistance to high temperatures is rooted in its unique molecular architecture:
● Conjugated System: The imide bonds and aromatic rings form a conjugated network, dissipating thermal energy efficiently.
● Low Coefficient of Thermal Expansion (CTE): Minimal expansion under heat reduces dimensional changes, ensuring stability during thermal cycling.
● High Glass Transition Temperature (Tg): Most PI films exhibit Tg values > 300°C, maintaining stiffness and integrity even at elevated temperatures.
3. Performance Metrics and Technical Specifications3.1 Temperature Resistance RangePI tapes are classified based on their thermal endurance, with typical performance ranges summarized in Table 1.
Table 1: Temperature Performance of PI Tapes
Tape Type | Continuous Use Temp. (°C) | Short-Term Exposure (°C, 30 min) |
Standard PI Tape | -200 to +260 | +300 |
High-Performance PI Tape | -200 to +300 | +400 |
Specialty (e.g., Aerospace) | -200 to +350 | +450 |
3.2 Adhesion and Shear StrengthThe adhesive layer is a critical component. Silicone-based adhesives dominate due to their wide operating temperature range (-60°C to +250°C) and high shear strength. Table 2 illustrates typical adhesion properties.
Table 2: Adhesion and Strength Metrics
Property | Value | Test Method |
Peel Adhesion (N/cm) | 1.15–1.25 | IPC-TM-650 2.4.9 |
Shear Strength (MPa) | 5–8 | ASTM D1002 |
Breakdown Voltage (kV) | >6 | ASTM D149 |
3.3 Electrical Insulation PropertiesPI tape is classified as an H-level insulator, with dielectric constants of 3.1–3.5 at 103 Hz and extremely low dissipation factors (10⁻³). This ensures safety in high-voltage environments.
4. Adhesive Systems: Key to High-Temperature Performance4.1 Silicone-Based AdhesivesSilicone adhesives are preferred for PI tape due to their:
● Thermal Durability: Crosslinked silicone polymers maintain bond strength at >300°C.
● Low Surface Energy: Facilitates easy release without residue after high-temperature exposure.
● Compatibility with PI Films: Chemical inertness prevents degradation of the substrate.
4.2 Other Adhesive Types (Acrylic, Rubber)While silicone dominates, alternatives are used in specific applications:
● Acrylic Adhesives: Lower-temperature environments (≤200°C) with superior initial tack.
● Rubber-Based Systems: Temporary fixation or applications avoiding silicone contamination.
5. Case Study: Automotive Industry Application5.1 Self-Adhesive Back Blocking Spray Paint TapeIn automotive manufacturing, PI tape is indispensable for high-temperature paint curing processes. For example, "lvmeikapton" PI tape with PET backing and silicone adhesive is used to protect underbody components during thermal spraying:
● Operating Conditions: Exposure to 200°C for 30–60 minutes.
○ Prevents paint overspray on critical areas.
○ Resists solvent侵蚀 from paint chemicals.
○ Removes cleanly without residue after curing.
5.2 Performance in Extreme ConditionsField tests demonstrate the tape's resilience:
● After 500 hours at 250°C, tensile strength retention: >90%.
● Peel adhesion post-thermal cycling: 1.2 N/cm (vs. initial 1.25 N/cm).
● No delamination or adhesive transfer during removal.
6. Applications in Electronics and Industrial Settings6.1 Wave Soldering Protection in PCBsPI tape shields gold fingers and sensitive components from molten solder (260°C–300°C). Its electrical insulation prevents shorts, while high tensile strength withstands mechanical stress during assembly.
6.2 Motor and Transformer InsulationIn H-class motors, PI tape缠绕线圈s to endure prolonged operation at 180°C–200°C. Its thin profile (0.03–0.1 mm) allows tight winding without compromising thermal dissipation.
6.3 Chemical and Radiation ResistancePI tape's resistance to acids, alkalis, and radiation makes it suitable for nuclear reactor cable insulation and semiconductor fabrication equipment protection.
7. Comparative Analysis: PI Tape vs. Alternative Materials
Material | Max Temp. (°C) | Adhesion | Chemical Resistance | Cost |
PI Tape | 400+ | High | Excellent | Moderate |
PTFE Tape | 260 | Low | Good | High |
Glass Fiber Tape | 350 | Medium | Fair | Low |
Kapton Film | 400+ | N/A (No adhesive) | Superior | High |
PI tape offers a balance of performance and cost, surpassing PTFE and glass fiber in adhesion and chemical resistance.
8. Future Developments and InnovationsOngoing research targets:
● Nanocomposite Adhesives: Incorporating ceramic nanoparticles to boost thermal conductivity and adhesion.
● UV-Curable PI Films: Rapid curing for high-speed manufacturing.
● Bio-Based PI Derivatives: Sustainable alternatives using renewable diamine sources.
9. ConclusionPolyimide tape’s efficacy in high-temperature environments is a synergy of its molecular structure, advanced adhesive systems, and engineering design. By combining thermal stability, robust adhesion, and electrical insulation, PI tape enables reliable performance in automotive, electronics, and industrial sectors. As technologies demand increasingly stringent thermal conditions, innovations in PI tape materials will continue to drive advancements across critical applications.
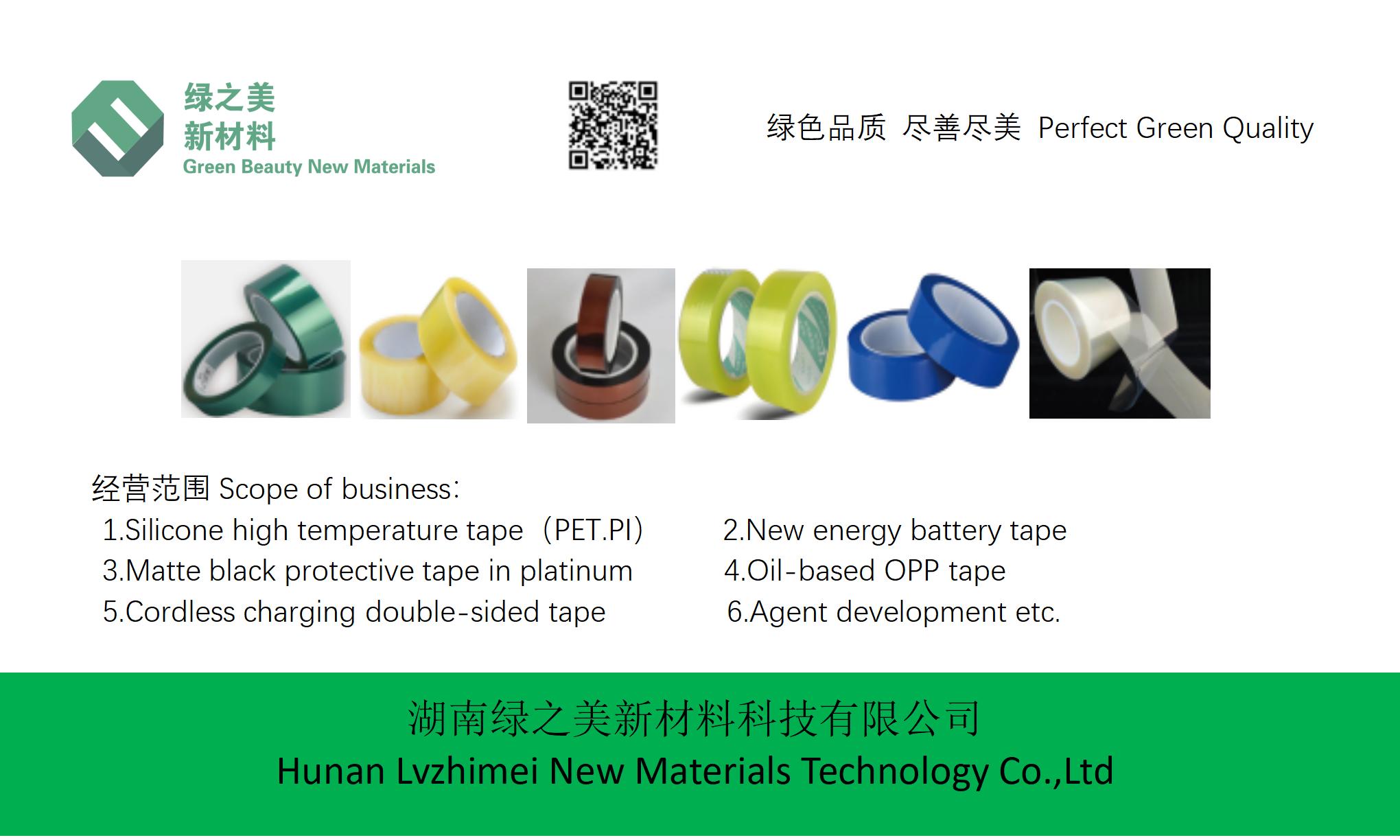