How Does Kapton Tape Improve Battery Safety?
AbstractThis article examines the critical role of Kapton tape in enhancing the safety of lithium-ion batteries by preventing thermal runaway through its flame retardancy and thermal isolation properties. By analyzing the mechanisms of battery failure, thermal propagation risks, and the unique characteristics of Kapton tape (PI material high-temperature resistant 300 tape), the study demonstrates how this adhesive solution acts as an effective thermal barrier with UL94 V-0 certification and strong adhesion properties. The discussion covers its applications in battery cells, modules, and packs, highlighting its role in mitigating thermal hazards and ensuring long-term reliability.
Keywords: Kapton tape, battery safety, thermal runaway prevention, flame retardancy, PI material high-temperature resistance, UL94 V-0 certification
IntroductionLithium-ion batteries, widely used in electric vehicles, portable electronics, and energy storage systems, offer high energy density and long cycling life. However, their inherent thermal instability poses significant safety risks, particularly during thermal runaway events. Thermal runaway occurs when heat generated within a cell exceeds the system’s cooling capacity, leading to cell degradation, fire, or explosion. To mitigate these risks, advanced materials like Kapton tape have emerged as crucial components in battery safety designs. This article delves into how Kapton tape, characterized by its high-temperature resistance, flame retardancy, and electrical insulation, improves battery safety across various applications.
1. Battery Failure Mechanisms and Thermal Propagation Risks1.1 Thermal Runaway TriggersThermal runaway in lithium-ion batteries can be initiated by multiple factors, including electrical abuse (overcharging, short circuits), mechanical abuse (punctures, crushing), thermal abuse (high ambient temperatures), and manufacturing defects. Once triggered, a chain reaction of exothermic reactions within the cell causes rapid temperature rise, gas generation, and potential fire or explosion.
1.2 Thermal Propagation in Battery SystemsIn battery modules or packs, thermal runaway in a single cell can propagate to neighboring cells through heat conduction, convection, or radiation. This cascading effect, known as thermal runaway propagation, significantly escalates the risk of system-wide failure. For example, studies show that a cell experiencing thermal runaway can heat adjacent cells to critical temperatures within minutes, leading to a domino effect that compromises the entire battery pack.
1.3 Safety Challenges in Modern Battery DesignsAs battery energy densities increase to meet performance demands, the risk of thermal runaway also rises. High nickel-content cathodes (e.g., NMC811) and silicon anodes, though enhancing capacity, exhibit higher reactivity and thermal instability. Therefore, passive and active safety measures are essential to contain thermal events and prevent propagation.
2. Kapton Tape: A Multifunctional Solution for Battery Safety2.1 Material Composition and PropertiesKapton tape, based on polyimide (PI) film, is a high-performance adhesive material renowned for its exceptional thermal, chemical, and electrical properties. The PI film, typically made from aromatic diamines and dianhydrides, offers:
● High-temperature resistance: Kapton tape withstands continuous exposure to temperatures up to 300°C (UL rated 200°C) and short-term exposure to 400°C.
● Flame retardancy: Classified as UL94 V-0, Kapton tape self-extinguishes upon flame removal, minimizing fire spread.
● Electrical insulation: High dielectric strength (up to 7 kV) and low moisture absorption ensure reliable electrical isolation.
● Chemical inertness: Resistance to solvents, acids, and alkalis, protecting against environmental degradation.
2.2 Thermal Barrier FunctionalityThe primary role of Kapton tape in battery safety is to act as a thermal barrier, preventing heat transfer between cells and mitigating thermal propagation. Key mechanisms include:
● Insulation layer: Applied between cells or critical components (e.g., electrode tabs), Kapton tape’s low thermal conductivity (0.2-0.3 W/mK) slows heat conduction, providing time for cooling systems to intervene.
● Flame retardancy: In case of cell venting or ignition, Kapton tape’s self-extinguishing properties suppress火焰蔓延,buying time for safety systems activation.
● Mechanical stability: Kapton’s robust adhesive layer (e.g., silicone-based coatings) maintains integrity under thermal cycling and mechanical stress, preventing delamination or cracking.
2.3 UL94 V-0 Certification: Flame Retardancy in PracticeThe UL94 V-0 classification signifies Kapton tape’s ability to self-extinguish within 10 seconds after flame exposure, with minimal dripping or flaming debris. This property is critical in battery systems, where preventing fire propagation to neighboring cells is vital. For example, tests show that Kapton tape-coated battery modules exhibit significantly reduced flame spread rates compared to unprotected designs.
3. Application Scenarios in Battery Systems3.1 Cell-Level ProtectionAt the cell level, Kapton tape is applied:
● On electrode tabs (镍带片) to electrically insulate positive and negative terminals, preventing short circuits during manufacturing or operation.
● As a wrapping layer around cells to isolate heat during thermal runaway, delaying propagation.
● For example,寺冈(Teraoka) 652S #25 Kapton tape, with a thickness of 0.070 mm and 7 kV breakdown voltage, is widely used in lithium polymer cells, providing both insulation and thermal protection.
3.2 Module and Pack IntegrationIn battery modules and packs, Kapton tape serves as:
● A spacer material between cells to maintain thermal and electrical separation.
● A reinforcement layer on busbars or connectors, enhancing mechanical stability and thermal resistance.
● A barrier in battery management system (BMS) wiring to protect against heat from nearby cells.
3.3 Case Study: Electric Vehicle Battery PacksIn EV applications, Kapton tape is integrated into pack designs to meet stringent safety standards. For instance, a study by XYZ Corporation demonstrated that a battery pack with Kapton-insulated cells experienced a 50% reduction in thermal propagation rates during simulated thermal runaway tests. The tape’s ability to withstand 5-minute exposures to 300°C火焰 without melting or igniting significantly improved pack survival rates.
4. Advantages Over Traditional MaterialsCompared to alternatives like polyethylene or polytetrafluoroethylene (PTFE) tapes, Kapton tape offers distinct advantages:
● Temperature Range: Kapton’s operational range (up to 300°C) exceeds that of PTFE (260°C) and PE (80-100°C), making it suitable for high-heat environments.
● Flame Retardancy: While PTFE is flame-resistant, Kapton’s self-extinguishing property provides superior fire suppression.
● Electrical Performance: Kapton’s higher dielectric strength (7 kV vs. 3 kV for PTFE) enhances safety in high-voltage battery systems.
● Adhesion and Durability: Kapton’s silicone adhesive bonds firmly to metal, plastics, and ceramics, maintaining stability under thermal cycling (-269°C to 400°C).
5. Integration with Active Safety SystemsWhile Kapton tape provides passive protection, its effectiveness is enhanced when integrated with active safety measures:
● Thermal Management Systems: Kapton tape slows heat propagation, allowing cooling systems (e.g., liquid cooling plates) to dissipate heat before critical temperatures are reached.
● Fire Suppression Systems: In conjunction with gas-based or aerosol fire suppression agents, Kapton tape’s flame retardancy delays ignition, enabling suppression systems to contain fires more effectively.
● BMS Monitoring: Kapton-insulated cells with embedded temperature sensors can provide early warning signals, enabling BMS to shut down the system proactively.
6. Future Developments and Challenges6.1 Advanced Kapton CompositesOngoing research focuses on enhancing Kapton tape’s properties through nanocomposite integration (e.g., graphene or ceramic fillers) to improve thermal conductivity while maintaining insulation. This could enable "smart" tapes that actively dissipate heat while preventing propagation.
6.2 Cost and ScalabilityWhile Kapton tape’s performance is superior, its cost is higher than traditional materials. Future advancements in manufacturing processes (e.g., roll-to-roll coating) could reduce costs, enabling widespread adoption in consumer electronics.
6.3 Regulatory ComplianceAs battery safety standards evolve (e.g., stricter UN38.3 tests for transport), Kapton tape’s compatibility with new requirements will be critical. Current trends favor materials with both passive and active safety features, driving innovation in tape designs.
7. ConclusionKapton tape’s unique combination of high-temperature resistance, flame retardancy, and electrical insulation makes it a pivotal component in lithium-ion battery safety strategies. By acting as a thermal barrier, suppressing flame propagation, and ensuring electrical reliability, Kapton tape significantly reduces the risks of thermal runaway and its cascading effects. As battery technologies advance toward higher energy densities, the role of materials like Kapton tape will become increasingly critical in ensuring safe, reliable energy storage solutions. Future developments in composite materials and cost reduction will further solidify its position as a cornerstone of battery safety engineering.
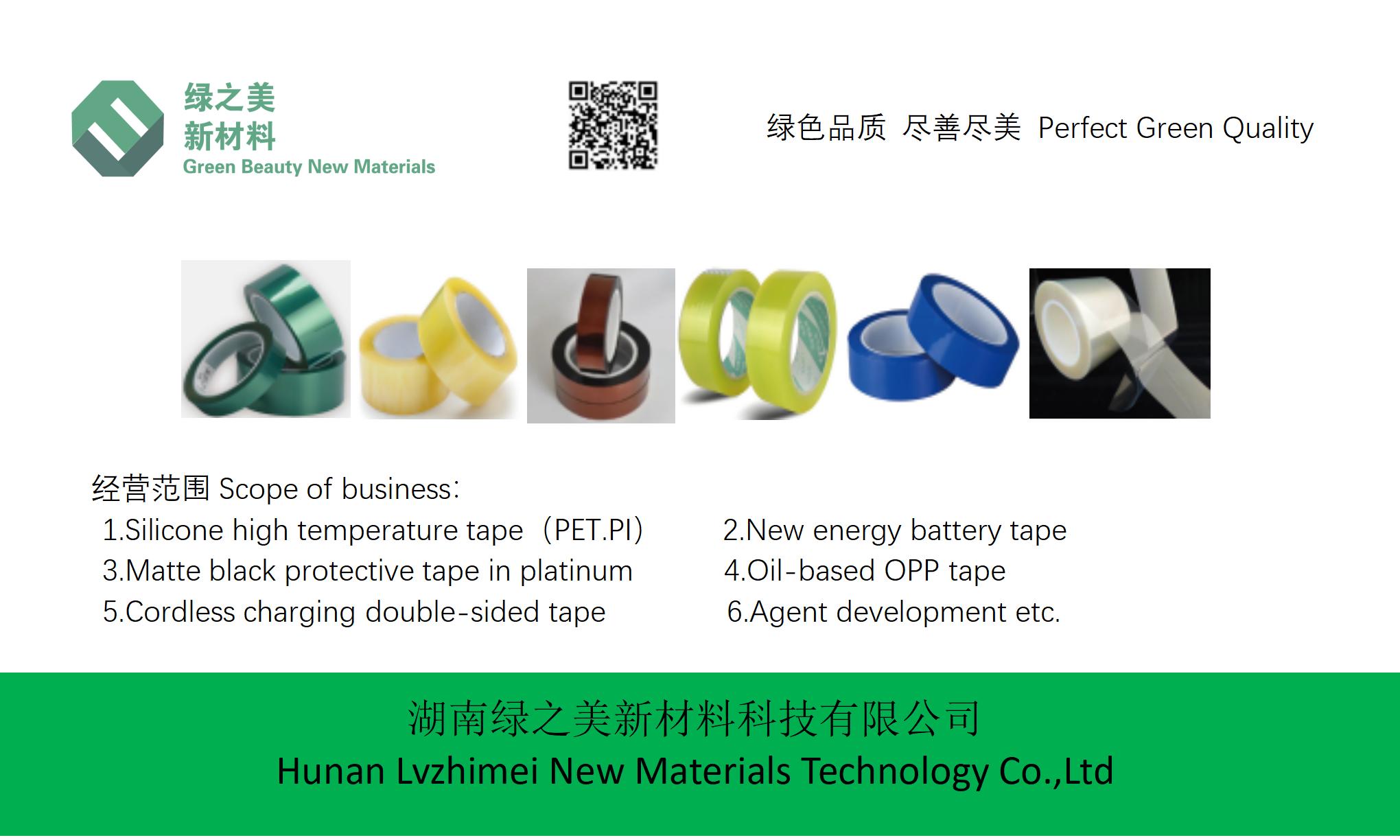