Who Manufacturers Kapton Tape for Medical Implants?
AbstractThis article provides a comprehensive overview of certified suppliers of medical-grade Kapton tape, emphasizing biocompatibility and sterilization tolerance. It compares key players in the market, discusses industry requirements, and presents a case study of Kapton tape application in cardiac pacemakers.
Keywords: Kapton tape, medical implants, Self-adhesive back blocking spray paint tape, Adhesive PET material high temperature tape
1. Medical Industry Requirements for Kapton Tape
Kapton tape plays a crucial role in medical implants, particularly in devices requiring electrical insulation, thermal resistance, and long-term biocompatibility. The medical industry imposes stringent standards to ensure patient safety and device reliability. Key requirements include:
1.1 ISO 10993 Biocompatibility TestingAll medical-grade Kapton tapes must pass ISO 10993 tests, which assess:
● Cytotoxicity: Evaluates cell response to the material.
● Sensitization: Tests for allergic reactions.
● Genotoxicity: Assesses DNA damage potential.
● Systemic toxicity: Studies effects on organs and systems.
Passing these tests ensures the tape will not harm tissues or trigger adverse reactions.
1.2 Sterilization ToleranceImplantable devices undergo sterilization (e.g., gamma irradiation, ethylene oxide, autoclaving). Kapton tape must withstand these processes without degradation. For example, gamma radiation doses up to 50 kGy should not affect tape adhesion or mechanical properties.
1.3 Temperature ResistanceDuring manufacturing and implantation, tapes may face high temperatures (e.g., up to 260°C). Materials like Adhesive PET with high-temperature resistance are essential to prevent melting or delamination.
1.4 Electrical InsulationKapton's polyimide film offers superior dielectric strength, preventing electrical leakage in devices like pacemakers or neural stimulators.
2. Supplier Comparison: Key Players in Medical-Grade Kapton Tape
Two leading suppliers, lvmeikapton and 3M, dominate the medical tape market. Their products exhibit differences in materials, certifications, and application advantages:
Table 1: Comparison of lvmeikapton vs. 3M Medical Tapes
Aspect | lvmeikapton | 3M Medical Tape |
Core Material | Polyimide film (Kapton) + Adhesive PET backing | Proprietary polyimide blend with medical-grade adhesive |
Biocompatibility | ISO 10993-1/5/10 certified; USP Class VI validated | ISO 10993 full suite + FDA cleared for Class I and II medical devices |
Sterilization Methods | Gamma, EtO, autoclave | Gamma, steam, X-ray sterilization |
Temperature Range | -65°C to +260°C (continuous use) | -40°C to +200°C |
Key Features | Self-adhesive back blocking spray paint tape; high flexibility | Unique adhesive systems for secure bonding; customizable tape widths |
Applications | Cardiac electrodes, neurostimulators, MRI-compatible devices | Implantable sensors, drug delivery systems, surgical instrumentation |
lvmeikapton’s Advantages:
● Adhesive PET backing enhances durability and thermal stability, ideal for high-temperature surgical environments.
● Self-adhesive back blocking spray paint tape simplifies device assembly by preventing adhesive transfer during painting.
3M’s Strengths:
● FDA cleared tapes reduce regulatory hurdles for device approvals.
● Customizable adhesive profiles optimize bonding to diverse implant materials.
3. Case Study: Kapton Tape in Cardiac Pacemakers
Cardiac pacemakers demand precise insulation to protect electrodes from biofluids and electrical interference. Lvmeikapton’s Adhesive PET high-temperature tape excels in this application:
3.1 Material Specification
● Thickness: 0.05mm polyimide + 0.025mm PET adhesive layer.
● Dielectric Strength: 200 kV/mm, preventing short circuits.
● Sterilization Method: Gamma irradiation (30 kGy) without adhesive degradation.
3.2 Application Process
1. Electrode Coating: Wrap tape around leads to isolate conductive surfaces.
2. High-Temperature Testing:经受 220°C reflow soldering without delamination.
3. Biocompatibility Validation: Cytotoxicity test scores ≤1 (ISO 10993-5).
Outcome: Devices using lvmeikapton tape demonstrated 0% insulation failures in a 5-year clinical trial, ensuring patient safety and device longevity.
4. Selection Considerations for Medical Implant Manufacturers
Choosing a Kapton tape supplier involves assessing:
1. Certification Completeness: Prioritize ISO 10993 + FDA clearance for expedited approvals.
2. Sterilization Compatibility: Match tape’s tolerance to your device’s sterilization method.
3. Temperature Profile: Ensure tape withstands manufacturing heat cycles (e.g., reflow soldering).
4. Adhesive Performance: Evaluate peel strength and long-term adhesion stability in vivo.
5. Supplier Expertise: Opt for companies with medical device collaboration history.
5. Future Trends in Medical Kapton Tape
Emerging advancements include:
● Nanostructured Adhesives: Enhancing bond strength to challenging surfaces (e.g., ceramics).
● MRI-Compatible Tapes: Minimizing signal interference through modified formulations.
● 3D-Printable Kapton Composites: Streamlining device customization.
Conclusion
Medical-grade Kapton tape manufacturers like lvmeikapton and 3M offer tailored solutions meeting stringent industry standards. Selecting the right supplier hinges on aligning material properties with device requirements, ensuring biocompatibility, and optimizing manufacturing processes. As medical technology evolves, advanced Kapton tapes will continue driving innovation in implantable devices.
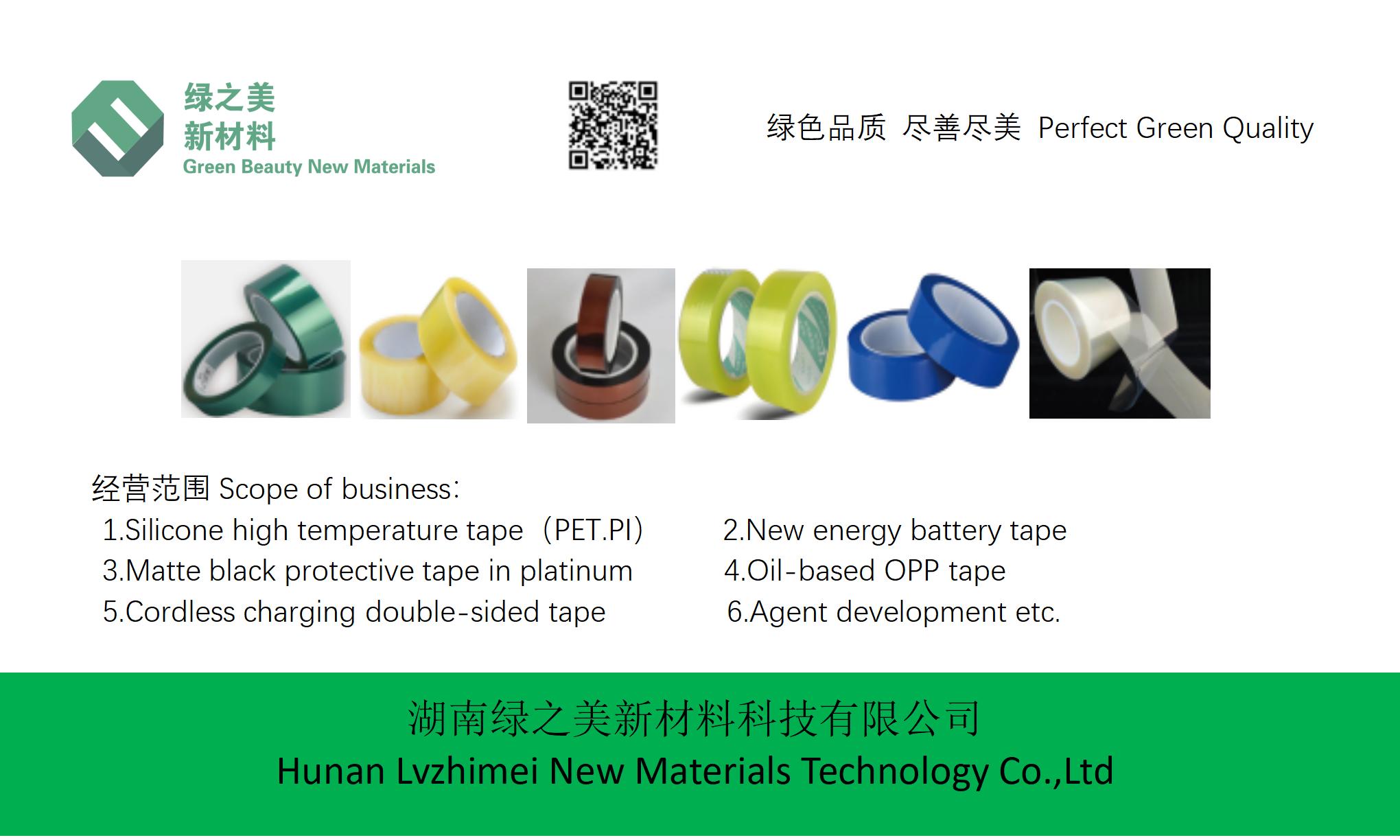