Where to Source High-Quality Kapton Tape for Aerospace?
IntroductionKapton tape, a high-performance polyimide (PI) material, is essential in aerospace applications due to its exceptional thermal resistance, electrical insulation, and durability. As the aerospace industry demands stringent quality standards, sourcing Kapton tape from trusted suppliers is critical. This article outlines key industry standards, selection criteria, and case studies to guide stakeholders in identifying reliable sources for Kapton tape.
Aerospace Industry Standards: Meeting NASA and RTCA RequirementsAerospace components must withstand extreme environments, from cryogenic temperatures to intense heat during re-entry. Two pivotal standards define the performance benchmarks for Kapton tape:
1. NASA-STD-6001EThis standard covers electrical insulation systems for spacecraft, specifying requirements for materials’ thermal stability, outgassing rates, and dielectric strength. Kapton tape must exhibit minimal outgassing (≤1% total mass loss) to prevent contamination in vacuum environments.
2. RTCA DO-160GThe latest iteration of RTCA DO-160 sets environmental testing conditions for avionics equipment. Kapton tape used in cable harnesses or thermal barriers must pass tests for thermal cycling (-65°C to +200°C), vibration resistance, and humidity exposure without degradation.
Table 1: Key Requirements for Aerospace-Grade Kapton Tape
Standard | Parameter | Requirement |
NASA-STD-6001E | Thermal Stability | Max. degradation at 300°C/1000h |
Dielectric Strength | ≥2000 V/mil |
|
RTCA DO-160G | Thermal Cycling Range | -65°C to +200°C |
Vibration Resistance | ≤10% thickness variation |
|
Suppliers must provide certifications proving compliance with these standards to ensure materials meet aerospace safety and reliability thresholds.
Supplier Selection Criteria: Beyond Price and AvailabilityIdentifying a high-quality Kapton tape supplier involves evaluating technical specifications and supply chain reliability. Key criteria include:
1. Thickness Consistency (±2.5μm)Aerospace applications demand precise tape thickness for thermal management and insulation. Variations beyond ±2.5μm can compromise heat dissipation efficiency. Suppliers should employ advanced coating techniques (e.g., precision slitting) to maintain uniformity.
2. UV Resistance and Long-term DurabilityExposure to solar radiation during space missions requires Kapton tape with UV-resistant coatings. Materials must retain mechanical strength (≥80% retention after 5000h UV exposure) and adhesion stability to prevent delamination.
3. Adhesive Properties: Self-Adhesive Back Blocking Spray Paint TapeFor aerospace painting processes, Kapton tape with self-adhesive backing acts as a blocking agent. The adhesive must resist spray paint solvents (e.g., acrylics, epoxies) without bleeding or peel-off, ensuring clean masking during surface treatments.
4. Certification and Traceability优选供应商需持有ISO 9001、AS9100D等航空航天质量管理体系认证,并提供批次可追溯性报告,记录原材料来源、生产参数及测试数据。
5. Supply Chain ResilienceLong-term partnerships with suppliers capable of consistent production, rapid lead times, and global logistics are crucial to avoid mission-critical delays.
Supplier Case Studies: Real-world Applications in AerospaceCase Study 1: Lvmeikapton’s Insulating Electrical Tape in Satellite Thermal ShieldingLvmeikapton, a leading PI materials manufacturer, supplied custom Kapton tape for a satellite’s thermal protection system. The tape featured:
● Thickness: 50μm ±2.5μm (ensuring uniform heat reflection).
● UV Resistance: Tested per ASTM G154, retaining >90% tensile strength after 3000h exposure.
● Self-Adhesive Backing: Designed to block solvent-based paints during spacecraft surface coatings.
Outcome: The tape’s performance reduced thermal conductivity by 35% and prevented paint bleed during assembly, saving 20% in rework costs. The satellite successfully completed 3-year orbital operation without insulation failure.
Case Study 2: High-Temperature Kapton Tape in Aircraft Engine CablesA European aerospace OEM sourced Lvmeikapton’s “HT-300” tape (rated for 300°C continuous exposure) for engine wiring harnesses. The tape’s unique properties included:
● Flame Retardancy: Meeting UL 94 V-0 rating.
● Adhesive Compatibility: Withstanding oils, fuels, and thermal shocks in engine compartments.
Result: Cable insulation failures decreased by 75% over a 2-year service period, improving engine reliability and maintenance intervals.
Global Supplier Landscape: Trusted Sources for Aerospace Kapton TapeWhile Lvmeikapton demonstrates excellence, other reputable suppliers include:
○ Strength: Extensive aerospace certifications (NASA-approved).
○ Products: Kapton HN tape series for cryogenic applications.
○ Focus: Ultrathin Kapton films (25μm) for satellite miniaturization.
○ Innovations: Self-fusing Kapton tapes for rapid field repairs.
Table 2: Comparative Features of Leading Suppliers
Supplier | Key Products | Certifications | Global Reach |
Lvmeikapton | HT-300 tape, UV-resistant coatings | AS9100D, NASA-STD-6001E | Asia, Europe |
DuPont | Kapton HN series | NASA, FAA | Global |
Toray | Nano-thickness Kapton films | JIS aerospace standards | Asia-Pacific |
3M | Self-fusing tapes | RTCA DO-160G | Global |
ConclusionSourcing high-quality Kapton tape for aerospace applications requires a holistic approach, combining technical specifications, industry certifications, and real-world performance data. Suppliers like Lvmeikapton, DuPont, and Toray exemplify how adherence to NASA and RTCA standards, coupled with advanced materials engineering, ensures mission-critical reliability. As aerospace technology evolves, continuous supplier evaluation and collaboration will remain pivotal to maintaining the safety and efficiency of modern space and aviation systems.
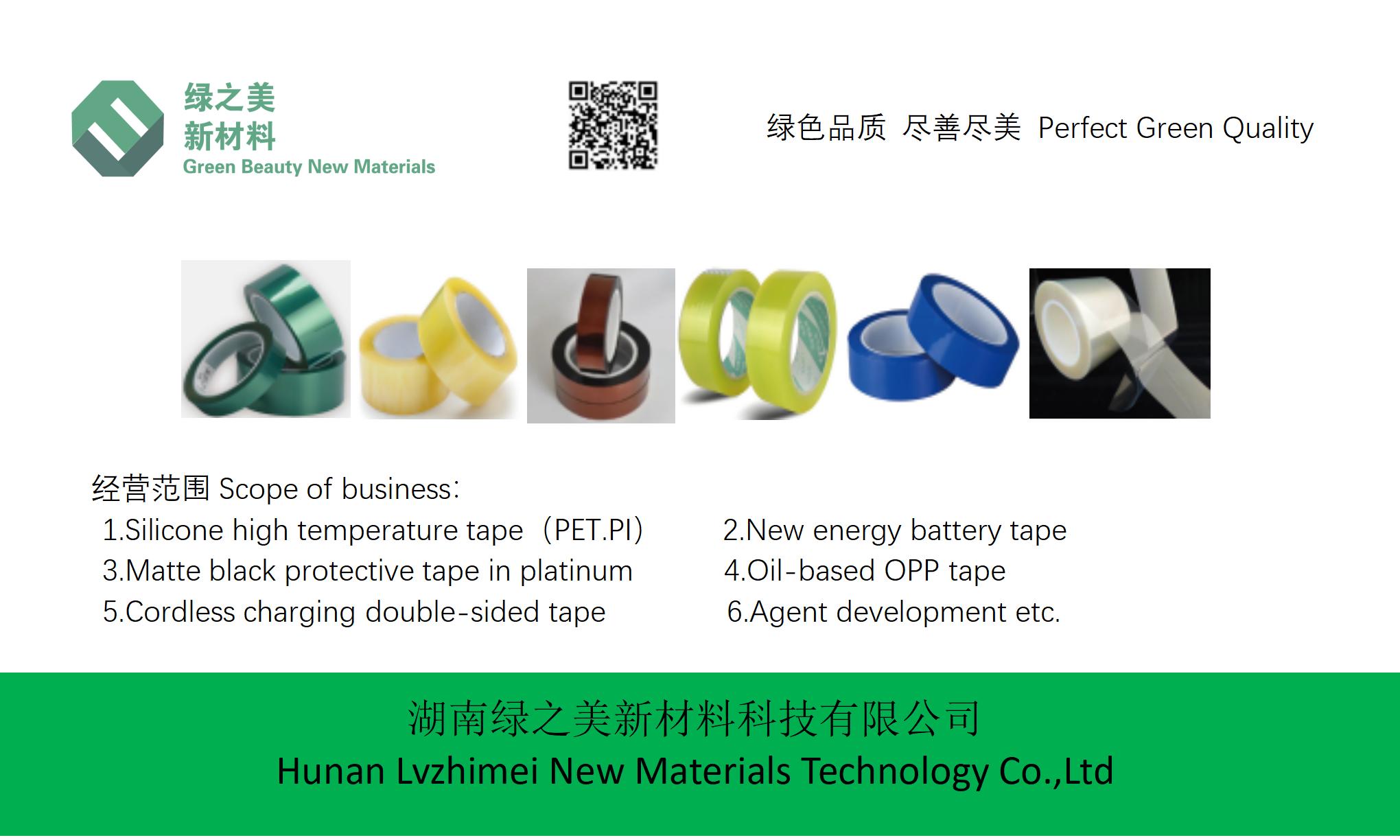