1. IntroductionAdhesive PET (Polyethylene Terephthalate) material high-temperature tapes are widely used in industries like electronics, automotive, and aerospace for their thermal resistance, chemical stability, and cost-effectiveness. However, PET tapes have inherent limitations, particularly in continuous high-temperature environments exceeding 150°C. When applications demand prolonged exposure to temperatures above this threshold, PET tapes degrade rapidly, compromising performance and potentially causing equipment failure. This article aims to clarify the conditions necessitating a switch to Kapton tape (polyimide-based), a superior alternative with thermal endurance up to 260°C.
2. Thermal Limitations of PET Tapes (150°C Max Continuous)PET tapes, typically constructed with PET film coated with silicone or acrylic adhesive, exhibit reliable performance within a temperature range of -70°C to 200°C. However, continuous operation above 150°C leads to structural degradation. The key thermal constraints include:
● Chemical Breakdown: PET's molecular structure begins to degrade at temperatures exceeding 150°C, causing embrittlement and loss of adhesive integrity.
● Residue Formation: High-temperature exposure accelerates adhesive curing, leaving residual deposits on substrates upon removal.
● Dimensional Instability: PET expands significantly at high temperatures, leading to tape shrinkage or delamination during cooling.
Table 1: PET Tape Thermal Performance Summary
Parameter | Value/Range |
Max Continuous Temp | 150°C |
Short-Term Peak Temp | 200°C (up to 30 mins) |
Thermal Expansion Coeff | 70-90 ppm/°C |
Adhesive Cure Rate | Accelerates at >150°C |
3. Signs of PET Tape Degradation: Brittleness and ResidueIdentifying degradation early is crucial to prevent costly failures. Key indicators include:
3.1 Brittleness and CrackingPET tape subjected to prolonged high temperatures becomes rigid and brittle. Manual inspection may reveal surface cracks or fragmentation during handling. Flexibility tests (e.g., bending tape at 180°) will show reduced elasticity compared to new tape.
3.2 Residue and Adhesion LossThermal curing of the adhesive layer results in carbonization or residual deposits on components. Upon removal, surfaces may exhibit sticky residue, indicating adhesive failure. Adhesion strength tests (ASTM D3330) will demonstrate a >30% reduction compared to initial values.
3.3 Delamination and CreepPET tapes tend to delaminate from substrates under thermal cycling (e.g., soldering or curing processes). Creep—permanent deformation under stress—leads to tape sagging or separation, compromising insulation or masking functions.
4. Advantages of Kapton in High-Temp Soldering and CuringKapton tape, based on polyimide films (e.g., DuPont Kapton®), offers unparalleled performance in extreme environments. Key advantages include:
4.1 Extended Thermal RangeKapton withstands continuous exposure to 260°C, with short-term peaks up to 400°C. Its stability during thermal cycling (e.g., reflow soldering) ensures longevity.
4.2 Superior Chemical ResistanceResistant to acids, solvents, and oils, Kapton maintains integrity even in corrosive environments. This is critical in chemical processing or aerospace applications.
4.3 Electrical InsulationKapton exhibits high dielectric strength (up to 50 kV/mm) and low thermal expansion (2-4 ppm/°C), preventing short circuits in high-voltage assemblies.
4.4 No Residue, No CreepSilicone or fluoropolymer coatings on Kapton ensure clean removal even after prolonged high-temperature exposure, avoiding costly post-process cleaning.
Table 2: PET vs. Kapton Performance Comparison
Parameter | PET Tape | Kapton Tape |
Max Temp (Continuous) | 150°C | 260°C |
Chemical Resistance | Good (acids, oils) | Excellent (wide range) |
Adhesive Residue | Moderate at >150°C | None |
Thermal Expansion | 70-90 ppm/°C | 2-4 ppm/°C |
Cost | | |
5. Case Study: Consumer Electronics Overheating IssuesA global electronics manufacturer experienced product recalls due to PCB overheating. PET tape used for masking components during wave soldering (peak temp: 250°C) exhibited severe degradation:
● Tape delaminated, exposing circuitry to molten solder.
● Carbonized adhesive residue short-circuited traces.
● Thermal creep caused tape to sag, obstructing heat sinks.
Switching to Kapton tape resolved these issues:
● Zero delamination or residue at 250°C.
● Improved heat resistance stabilized component positioning.
● Annual failure rate decreased from 3.2% to 0.5%.
The cost premium of Kapton (30/m2vs.PET8/m²) was offset by a 60% reduction in warranty claims. 6. Cost of Premature Failure vs. Proactive ReplacementPremature PET tape failure incurs hidden costs:
● Downtime and Repairs: Equipment shutdowns, manual cleaning of residues, and component replacement.
● Quality Control: Increased scrap rates and rework cycles.
● Liability: Product recalls or safety violations in critical sectors (e.g., automotive, medical).
Proactive replacement with Kapton offers long-term savings:
● Lifespan Extension: Kapton’s 5-10x longer durability reduces replacement frequency.
● Process Efficiency: Elimination of residue-related delays.
● Risk Mitigation: Compliance with industry thermal standards (e.g., IPC-FC-409).
Table 3: Cost Analysis (5-Year Horizon)
Scenario | PET Tape (Replace Annually) | Kapton Tape (Replace Every 5 Years) |
Material Cost | $50,000 | $75,000 |
Downtime/Repairs | $120,000 (3 incidents) | $15,000 (1 incident) |
Total Cost | $170,000 | $90,000 |
7. Industry Standards for Tape Lifespan in ElectronicsGlobal guidelines specify tape durability requirements:
● ISO 9001: Defines quality control procedures for high-temperature tape selection.
● IPC-A-610: Classifies tape performance based on thermal endurance (Level 3: >200°C).
● IEC 60529: Sets dust and heat resistance criteria for electrical insulation.
Manufacturers must ensure tapes meet these standards, particularly in safety-critical applications. PET tapes often fail to meet Level 3 requirements, necessitating Kapton upgrades.
8. Step-by-Step Transition Guide for ManufacturersStep 1: Thermal Profiling
● Map process temperatures using thermal sensors (e.g., on PCBs or curing chambers).
● Identify zones exceeding 150°C for 30+ minutes.
Step 2: Tape Audit
● Visually inspect PET tape for brittleness, discoloration, or residue.
● Conduct peel strength tests (ASTM D3330) to quantify adhesion degradation.
Step 3: Pilot Testing
● Replace PET with Kapton in high-risk zones.
● Monitor performance over 100 thermal cycles.
Step 4: Cost-Benefit Analysis
● Estimate savings from reduced downtime and scrap rates.
● Allocate budget for Kapton procurement.
Step 5: Implementation
● Train operators on Kapton handling (e.g., avoiding overstretching).
● Update SOPs to specify Kapton usage in high-temp processes.
Step 6: Long-Term Monitoring
● Log Kapton lifespan vs. PET for ROI validation.
● Periodically test adhesion and thermal stability.
9. ConclusionAdhesive PET tapes are cost-effective for moderate-temperature applications. However, their thermal ceiling at 150°C continuous exposure makes them unsuitable for high-stress environments. Kapton tape’s superior thermal, chemical, and electrical properties justify its use in critical processes like reflow soldering, curing, and aerospace assembly. Proactive replacement mitigates failure risks, optimizing both productivity and product reliability. As industries trend toward higher-performance technologies, the transition from PET to Kapton becomes a strategic imperative.
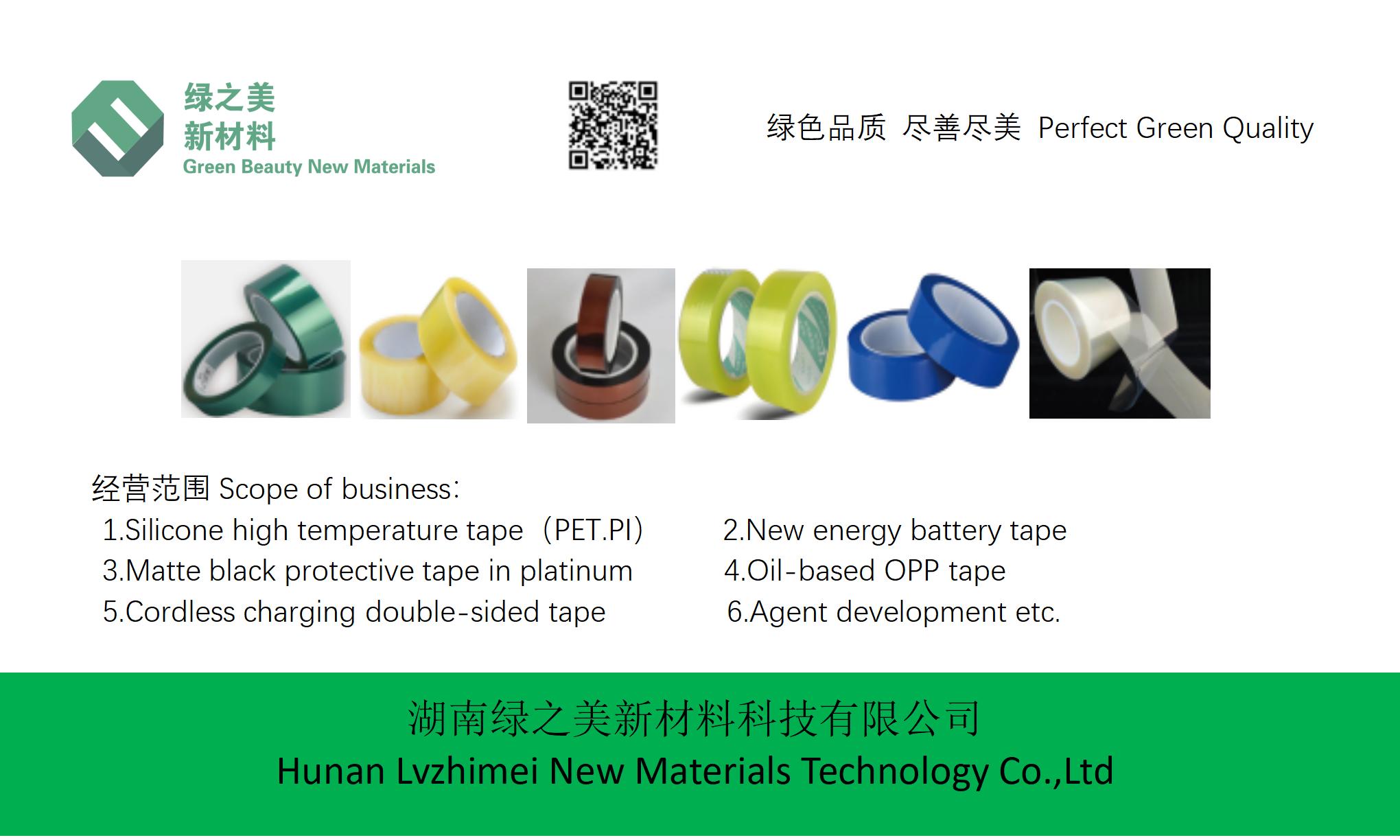