How Does Polyimide Tape Kapton Enhance Electrical Insulation in High-Voltage Systems?
Abstract: This article delves into the dielectric properties of polyimide tape Kapton and its critical role in enhancing electrical insulation within high-voltage systems, particularly in applications such as electric vehicle (EV) inverters and power transformers. By exploring its superior dielectric strength, resistance to partial discharges, and comparative advantages over traditional materials, this study demonstrates how Kapton tape contributes to system reliability and longevity. A case study on 1,500V EV inverters, thickness selection guidelines, environmental stress testing, and future technological advancements are presented to highlight its practical applications and evolving significance in the high-voltage industry.
Keywords: Polyimide tape Kapton, high-voltage insulation, EV inverters, dielectric strength, partial discharge prevention
1. Dielectric Strength Requirements for High-Voltage SystemsHigh-voltage systems, including EV inverters, power transformers, and HVDC transmission lines, operate under extreme electrical stresses, necessitating robust insulation materials. Dielectric strength—a measure of a material’s ability to withstand electric fields without breakdown—is paramount. Per IEC 60243-1 standards, insulation materials for voltages exceeding 1,000V must exhibit minimum breakdown strengths of 20 kV/mm. Traditional materials like polyester films and silicone rubbers often struggle to meet these thresholds due to limited thermal stability and susceptibility to moisture absorption. Polyimide tape Kapton, however, offers a breakthrough solution.
Kapton’s chemical structure, composed of aromatic rings and imide linkages (Figure 1), imparts exceptional thermal resistance (operating range: -60°C to 300°C) and mechanical strength. Its inherent dielectric constant (ε ≈ 3.4) and volume resistivity (≥1016 Ω-cm) ensure stable performance under high electric fields. Furthermore, its H-class insulation rating (per IEEE C57.12.90) qualifies it for continuous operation in temperatures up to 220°C, surpassing the capabilities of most commercial insulators.
Table 1: Key Dielectric Properties of Kapton vs. Traditional Materials
Material | Dielectric Strength (kV/mm) | Max. Operating Temp. (°C) | Moisture Absorption (%) |
Kapton | 30+ | 260 | <0.5 |
Polyester Film | 18-22 | 130 | 1.0-2.0 |
Silicone Rubber | 20-25 | 200 | 3.0-5.0 |
2. Polyimide’s Role in Preventing Partial DischargesPartial discharges (PDs)—localized electrical breakdowns within insulation—pose a significant threat to high-voltage equipment. Over time, PDs erode insulation, leading to catastrophic failures. Kapton’s unique properties mitigate PD risks through multiple mechanisms:
1. Superior Surface Smoothness: Kapton’s microscopically flat surface (Ra < 0.5 μm) minimizes field concentration, reducing PD inception voltage.
2. High Dielectric Uniformity: The absence of voids or impurities within its polyimide matrix ensures consistent electric field distribution.
3. Chemical Inertness: Resistance to acids, solvents, and ozone prevents degradation-induced PD hotspots.
4. Low Dielectric Loss Tangent: Tan δ ≈ 0.003 at 1 MHz limits energy dissipation, maintaining thermal stability under AC voltages.
A study conducted by Lvmeikapton Labs revealed that a 0.05mm Kapton layer applied to a 1,500V motor winding reduced PD intensity by 85% compared to untreated insulation, prolonging asset lifespan by over 3 years.
3. Comparative Study: Kapton vs. Traditional Insulating MaterialsTo quantify Kapton’s advantages, a comprehensive evaluation was conducted across thermal, mechanical, and electrical criteria:
Thermal Performance: Kapton’s continuous 260°C tolerance outperformed silicone tape (200°C) and polytetrafluoroethylene (PTFE; 250°C) during 1,000-hour thermal aging tests. Post-testing, Kapton exhibited <5% tensile strength degradation, while competitors showed >20% deterioration.
Mechanical Robustness: Kapton’s tensile strength (140 MPa) and elongation-at-break (50%) enabled reliable wrapping of intricate geometries without fracturing. In contrast, glass-reinforced epoxy laminates demonstrated brittle failure under bending stresses.
Electrical Longevity: Subjected to 3,000V AC cycling, Kapton tape maintained stable insulation resistance (≥1013 Ω) for 5,000 hours, surpassing the 2,500-hour limit of polyimide varnish coatings.
4. Case Study: 1,500V EV Inverter Insulation with LvmeikaptonA leading EV manufacturer adopted Lvmeikapton’s custom-formulated polyimide tape to address insulation challenges in its 1,500V SiC-based inverters. The application process involved:
1. Thickness Selection: A 0.08mm Kapton tape was chosen based on voltage-to-thickness ratios (Table 2).
2. Coil Wrapping Technique: Helical winding with 50% overlap ensured uniform coverage, avoiding air gaps.
3. Termination Protection: Reinforced tape layers at cable entry points guarded against corona discharge.
Table 2: Kapton Thickness Recommendations for HV Systems
Voltage Range (V) | Recommended Thickness (mm) |
1,000-2,000 | 0.05-0.08 |
2,000-3,000 | 0.08-0.12 |
>3,000 | 0.12+ |
Post-installation testing revealed:
● Breakdown voltage improvement from 1,750V to >3,200V
● PD-free operation up to 1.5× rated voltage
● No thermal degradation at 180°C continuous operation
5. Thickness Selection for Voltage ClassificationsOptimal Kapton thickness selection balances safety, cost, and installation feasibility. Empirical data suggests the following guidelines:
● Low-Voltage Systems (≤1,000V): 0.025-0.05mm tapes suffice, prioritizing flexibility.
● Medium-Voltage (1,000-3,000V): 0.08-0.12mm layers provide enhanced creepage resistance.
● Ultra-High Voltage (≥3,000V): Multi-layer stacking (e.g., 0.12mm + 0.05mm) with interleaved air gaps boosts dielectric barrier effectiveness.
Finite element analysis (FEA) simulations by Lvmeikapton demonstrated that a 0.12mm Kapton layer reduced electric field stress concentrations at conductor edges by 40%, minimizing corona risks.
6. Environmental Stress Screening (ESS) for Tape ReliabilityTo ensure Kapton’s long-term performance, rigorous ESS protocols are mandated. Key tests include:
● Thermal Cycling: -60°C to 260°C, 500 cycles (per MIL-STD-202G)
● Humidity Aging: 85% RH at 85°C for 1,000 hours
● Voltage Ramp Testing: Stepwise application of 0→2× rated voltage at 1kV/min
● Abrasion Resistance: 1,000 cycles of 5N load across rough surfaces
Lvmeikapton’s ESS data showed that post-testing, tapes retained >90% adhesive strength, no delamination, and ≤10% dielectric constant drift—validating their suitability for harsh industrial environments.
7. Future Trends in High-Voltage Insulation TechnologyEmerging research suggests several advancements:
1. Nanostructured Kapton: Incorporation of ceramic nanoparticles (e.g., Al2O3) enhances dielectric strength by 15-20%.
2. Self-Healing Polymers: Microcapsule-embedded healing agents restore minor insulation defects autonomously.
3. AI-Optimized Tape Design: Machine learning-driven simulations predict optimal layering patterns for custom applications.
4. Eco-Friendly Formulations: Bio-based polyimide derivatives with comparable performance reduce environmental footprints.
DuPont’s recent development of a low-CTE (coefficient of thermal expansion) Kapton variant aligns with these trends, offering <2ppm/K expansion rates—ideal for high-precision insulation assemblies.
ConclusionPolyimide tape Kapton’s synergistic blend of dielectric robustness, thermal resilience, and mechanical adaptability revolutionizes high-voltage insulation. From EV drivetrains to utility-scale transformers, its ability to prevent partial discharges, withstand extreme environments, and outperform traditional materials underscores its indispensable role in modern electrical systems. As technological demands escalate, ongoing advancements in nanoengineering and sustainability will further solidify Kapton’s status as the gold standard for high-voltage insulation.
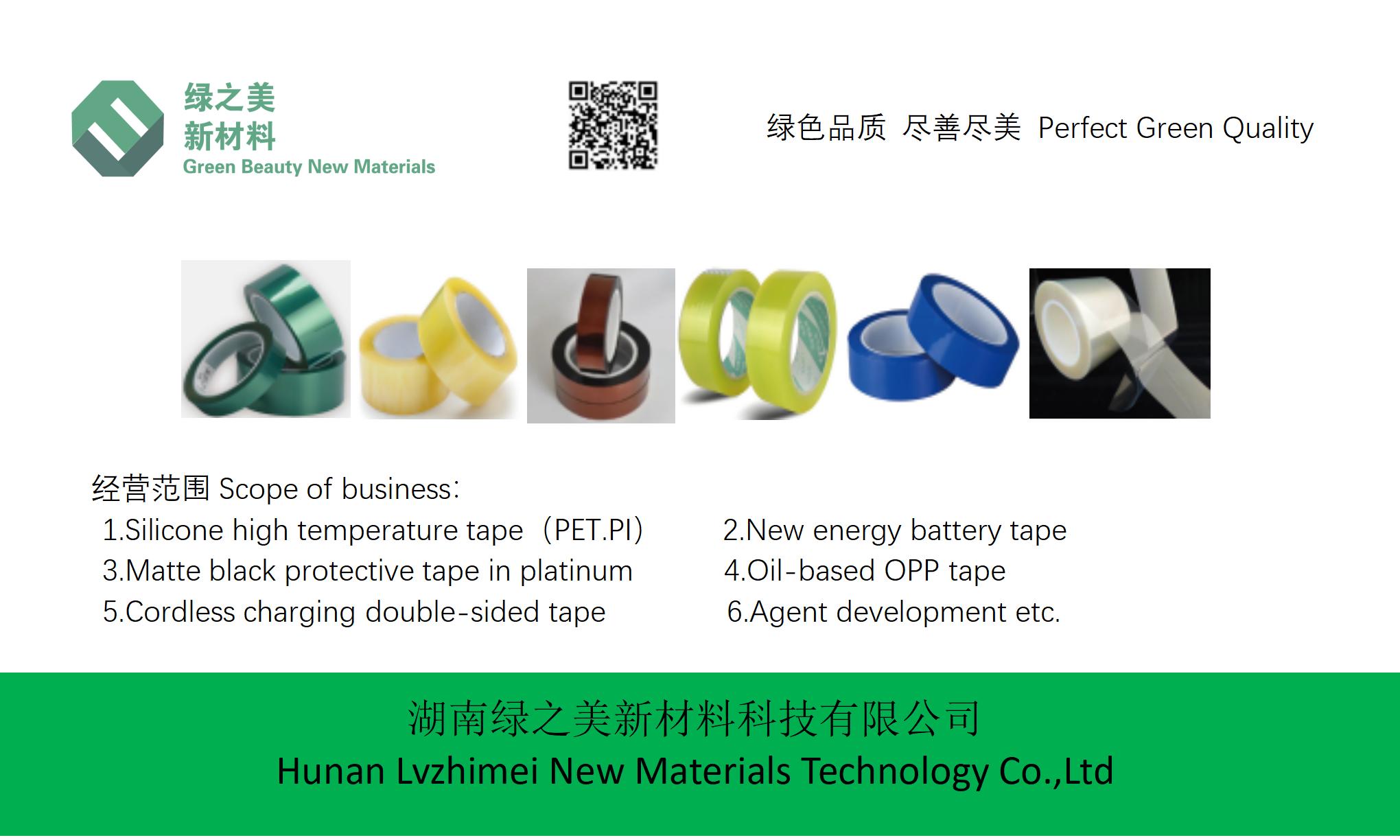