How to Choose the Right Polyimide Tape for Electronicshttps://www.lvmeikapton.com/
Title: How to Choose the Right Polyimide Tape for ElectronicsDescription: Explore the key factors to consider when selecting polyimide tape for electronics, including material properties, temperature resistance, and adhesive types.Keywords: Polyimide tape, Kapton, Gold finger electronics, High-temperature resistance, Adhesion
Content:
In the electronics industry, choosing the right tape is crucial for ensuring durability and performance. Polyimide tape, known for its exceptional thermal stability and electrical insulation, is a popular choice. This guide explains how to select the ideal tape based on application needs.
1. Understanding Polyimide Tape: Key Material PropertiesPolyimide tape (commonly known as Kapton tape) is constructed using a polyimide film substrate coated with silicone adhesive. The film’s composition provides several critical advantages:
● Temperature Resistance: Polyimide tapes can withstand extreme temperatures, typically ranging from -100°F to 500°F (-73°C to 260°C). This makes them suitable for high-temperature processes like wave soldering, reflow soldering, and thermal cycling.
● Electrical Insulation: The tape exhibits excellent dielectric properties, protecting components from electrical arcing or short circuits.
● Chemical Resistance: It resists common solvents, acids, and alkalis, ensuring stability during manufacturing processes.
● Mechanical Strength: The film’s tear and abrasion resistance reduces the risk of damage during handling or assembly.
Table 1: Key Properties of Polyimide Tape
Property | Description |
Temperature Range | -100°F to 500°F (-73°C to 260°C) |
Dielectric Strength | 4.0 kV to 8.5 kV |
Adhesion to Steel | 22 oz./in. width (24 N/100mm) |
Tensile Strength | 33 lbs./in. width (578 N/100mm) |
Thickness Range | 0.05-0.20mm (35μm-180μm) |
2. Application ConsiderationsChoosing the right tape requires aligning its properties with specific application requirements.
2.1. Temperature Requirements
● Low-Temperature Environments: For applications below 200°C, standard polyimide tapes with silicone adhesive suffice.
● High-Temperature Processes: For soldering (e.g., wave soldering at 260°C) or thermal curing, select tapes with high-temperature resistance (e.g., "PI material high-temperature resistant 300 tape").
● Extreme Conditions: In aerospace or automotive electronics, tapes rated up to 500°F (e.g., "lvmeikapton insulating electrical tape") ensure reliability.
2.2. Adhesive TypesAdhesive selection impacts performance:
● Silicone Adhesive: Most common, offering high-temperature stability and easy release. Ideal for solder masking and temporary fixtures.
● Acrylic Adhesive: Provides stronger bonds for permanent applications like battery tab insulation.
● Pressure-Sensitive Adhesive (PSA): Self-adhering tapes suitable for static protection or flexible circuit board fixation.
Table 2: Adhesive Types Comparison
Adhesive Type | Temperature Range | Bond Strength | Release Properties | Applications |
Silicone | -100°F to 500°F | Medium | Easy release | Wave soldering, thermal curing |
Acrylic | -40°F to 400°F | High | Permanent | Battery insulation |
PSA | -20°F to 300°F | Variable | Self-adhering | Flexible PCB mounting |
2.3. Thickness and FlexibilityThinner tapes (e.g., 0.05mm) are suitable for intricate components, while thicker options (0.20mm) offer enhanced mechanical protection. Flexibility matters for applications like cable wrapping or conformal coating.
3. Specialized Applications in Electronics3.1. Printed Circuit Board (PCB) Protection
● Gold Finger Shielding: Polyimide tape masks gold contacts during wave soldering to prevent oxidation and damage.
● SMT Process: Tapes with silicone adhesive fix components during surface mounting, ensuring stability during reflow.
● Insulation: For high-voltage transformers or inverters, tapes with dielectric strengths up to 8.5 kV are essential.
3.2. Battery TechnologyIn lithium-ion batteries, polyimide tapes insulate electrode tabs, preventing short circuits. Acrylic adhesive tapes provide secure bonds in battery packs.
3.3. High-Temperature Processes
● Powder Coating: The tape’s heat resistance shields components during electrostatic spraying (up to 280°C).
● Electroplating: It acts as a barrier during电镀 processes, avoiding contamination.
4. Additional Considerations4.1. Shelf Life and StorageStore tapes at 60-80°F (15-21°C) and 40-50% RH to maintain adhesion. Most tapes retain optimal performance within 12 months of manufacture.
4.2. Certification and StandardsEnsure tapes meet industry standards (e.g., UL, RoHS) for electrical safety and environmental compliance.
4.3. Brand and Supplier SelectionChoose reputable brands like Kapton® or trusted manufacturers (e.g., SM by Dongguan Senma) offering customizable thicknesses and widths.
5. Cost vs. PerformanceWhile high-grade tapes may cost more ($9.90/piece), they reduce rework costs due to their durability. Evaluate long-term benefits over initial investment.
6. ConclusionSelecting the right polyimide tape requires a holistic assessment of temperature exposure, adhesive compatibility, mechanical demands, and regulatory compliance. By aligning these factors with application specifics, electronics manufacturers can optimize reliability, efficiency, and longevity of their products.
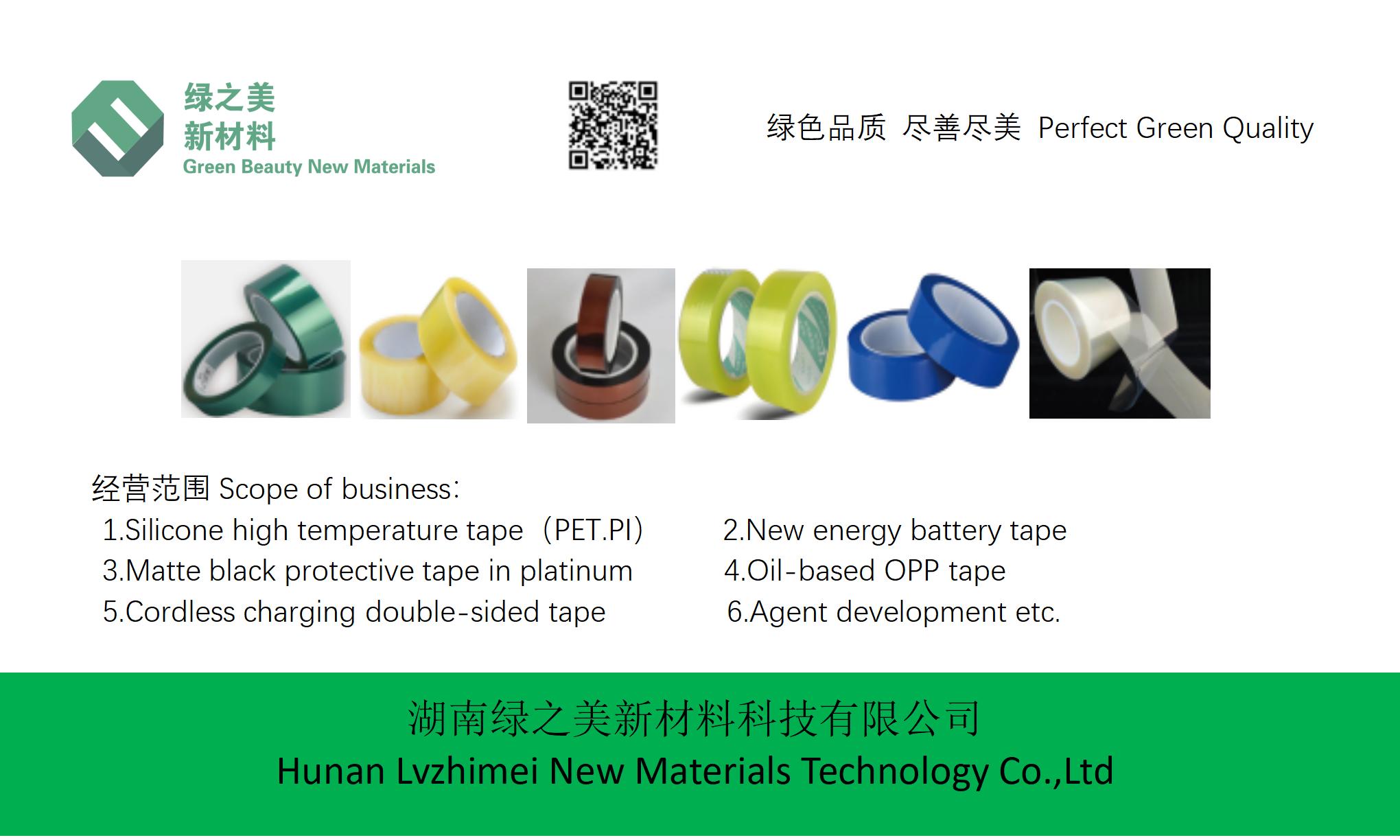