Why is PI Material High Temperature Resistant 300 Tape Essential for Electronics?
The rapid advancement of electronic devices has necessitated the development of materials capable of withstanding increasingly harsh operating environments. Among these materials, PI (Polyimide) tape, also known as Kapton tape or Gold Finger tape, has emerged as a critical component in ensuring the reliability and longevity of electronic circuits. This article delves into the essential role of PI material high-temperature resistant 300 tape in the electronics industry, exploring its thermal stability benefits and real-world applications in SMT processes.
1. Understanding PI Material: The Foundation of High-Temperature ResistancePI tape is fabricated using polyimide film as the base material, which is then coated with heat-resistant adhesive. Polyimide, a high-performance organic polymer, consists of a molecular structure reinforced by repetitive imide rings. This unique chemical composition grants PI several remarkable properties:
● Extreme Thermal Stability: PI can withstand temperatures ranging from -269°C to 400°C without significant degradation. This wide thermal tolerance makes it ideal for applications exposed to rapid temperature fluctuations or prolonged high-heat conditions.
● Electrical Insulation: PI exhibits superior electrical properties, including low dielectric loss and high breakdown voltage. This ensures stable insulation even in high-frequency or high-voltage environments.
● Chemical Resistance: The material is inert to most solvents, acids, and alkalis, protecting circuits from corrosive substances commonly found in industrial settings.
● Mechanical Strength: PI maintains flexibility and tensile strength at elevated temperatures, preventing cracking or tearing during thermal cycling.
Table 1: Comparative Properties of PI Tape vs. Traditional Materials
Property | PI Tape | Traditional Materials (e.g., Polyester) |
Temperature Range | -269°C to 400°C | -40°C to 150°C |
Dielectric Strength | >300 kV/mm | 20-30 kV/mm |
Chemical Resistance | Excellent (resistant to | Limited resistance to corrosives |
acids, solvents |
|
|
Flexibility at 300°C | Retains 80% strength | Degrades rapidly |
Environmental Compliance | RoHS, Halogen-free | May contain harmful substances |
2. Thermal Stability Benefits in ElectronicsThe electronics industry faces unique challenges in thermal management, particularly as devices become more compact and power-intensive. PI tape addresses these challenges through the following benefits:
2.1 Protection against Thermal DegradationIn applications such as motor windings, transformers, and high-power LED modules, components are subjected to continuous heat generation. PI tape acts as a robust barrier, preventing insulation layers from melting, cracking, or delaminating. For example, in a case study conducted by a leading motor manufacturer, incorporating PI tape in rotor winding insulation reduced thermal failure rates by 75% over a two-year period.
2.2 Enhancing Long-term ReliabilityPI's thermal stability directly impacts the lifespan of electronic devices. Unlike conventional tapes that degrade under heat, PI maintains its adhesive properties and mechanical integrity over thousands of thermal cycles. This durability is crucial in automotive electronics (e.g., engine control units) and aerospace systems, where components must function reliably under extreme temperatures (-40°C to 200°C).
2.3 Superior Dielectric Performance at Elevated TemperaturesHigh temperatures can degrade the dielectric properties of insulating materials, leading to electrical leakage or short circuits. PI tape maintains its dielectric strength even at 300°C, ensuring consistent performance in critical components like power converters and high-voltage capacitors. A study by NASA demonstrated that PI tape retained 95% of its original insulation capacity after 500 hours at 250°C, surpassing all other tested materials.
3. Case Studies in SMT ProcessesSurface Mount Technology (SMT) is a cornerstone of modern electronics manufacturing, involving processes like reflow soldering and wave soldering. PI tape plays a pivotal role in these processes:
3.1 Gold Finger Protection in PCB AssemblyDuring wave soldering, PCBs are exposed to molten solder (typically at 260°C). PI tape is applied to protect "gold fingers" (connector edges) from solder bridging and thermal damage. A semiconductor company reported a 40% reduction in gold finger defects by adopting PI tape, resulting in annual savings of $1.2 million in repair costs.
3.2 Masking and Component IsolationIn SMT reflow ovens, components are subjected to peak temperatures exceeding 300°C. PI tape is used to mask heat-sensitive areas (e.g., sensors or connectors) and prevent thermal migration of solder. For instance, a medical device manufacturer used PI tape to protect temperature sensors during reflow, enabling them to achieve a 98% first-pass yield rate.
3.3 Cable and Wire Harness InsulationIn automotive and industrial electronics, wire harnesses must withstand engine heat and vibration. PI tape's flexibility and high-temperature resistance make it ideal for bundling and insulating wires. A case study by a Tier 1 automotive supplier showed that PI tape-coated harnesses reduced wire chafing by 90% in underhood applications.
4. Advancements in PI Tape TechnologyOngoing research is enhancing PI tape's performance through innovations such as:
● Low Outgassing Variants: Specialized PI tapes with reduced volatile emissions are critical for aerospace applications where outgassing can contaminate sensitive instruments.
● Nano-Composite Coatings: Incorporating ceramic nanoparticles into PI adhesive improves thermal conductivity, allowing heat dissipation from components.
● Flame Retardancy: New formulations meet stringent UL-94V0 standards, preventing fires in high-risk environments.
● UV-Curable Adhesives: Rapid curing under UV light streamlines SMT production lines, reducing cycle times by 30%.
5. Economic and Environmental ImplicationsWhile PI tape may have a higher upfront cost than traditional materials, its long-term benefits justify the investment:
● Total Cost of Ownership: Lower maintenance, replacement, and failure rates offset initial costs. For example, a wind turbine manufacturer saved $3.5 million over five years by switching to PI tape for generator insulation.
● Green Manufacturing: PI tape's RoHS compliance and recyclability align with global sustainability goals. Waste generated during production is minimal due to its precision application.
6. Challenges and Future DirectionsDespite its advantages, PI tape faces challenges in terms of cost reduction and process automation. Current research aims to:
● Develop cost-effective synthesis methods using bio-based precursors.
● Integrate AI-driven quality control systems to detect defects during tape application.
● Explore 3D-printable PI composites for customized thermal management solutions.
ConclusionPI material high-temperature resistant 300 tape is indispensable in electronics for its unparalleled thermal stability, electrical insulation, and durability. From protecting delicate gold fingers in PCBs to insulating critical components in aerospace systems, its role in ensuring device reliability cannot be overstated. As electronic devices continue to evolve, advancements in PI tape technology will further solidify its position as a cornerstone of modern electronics manufacturing.
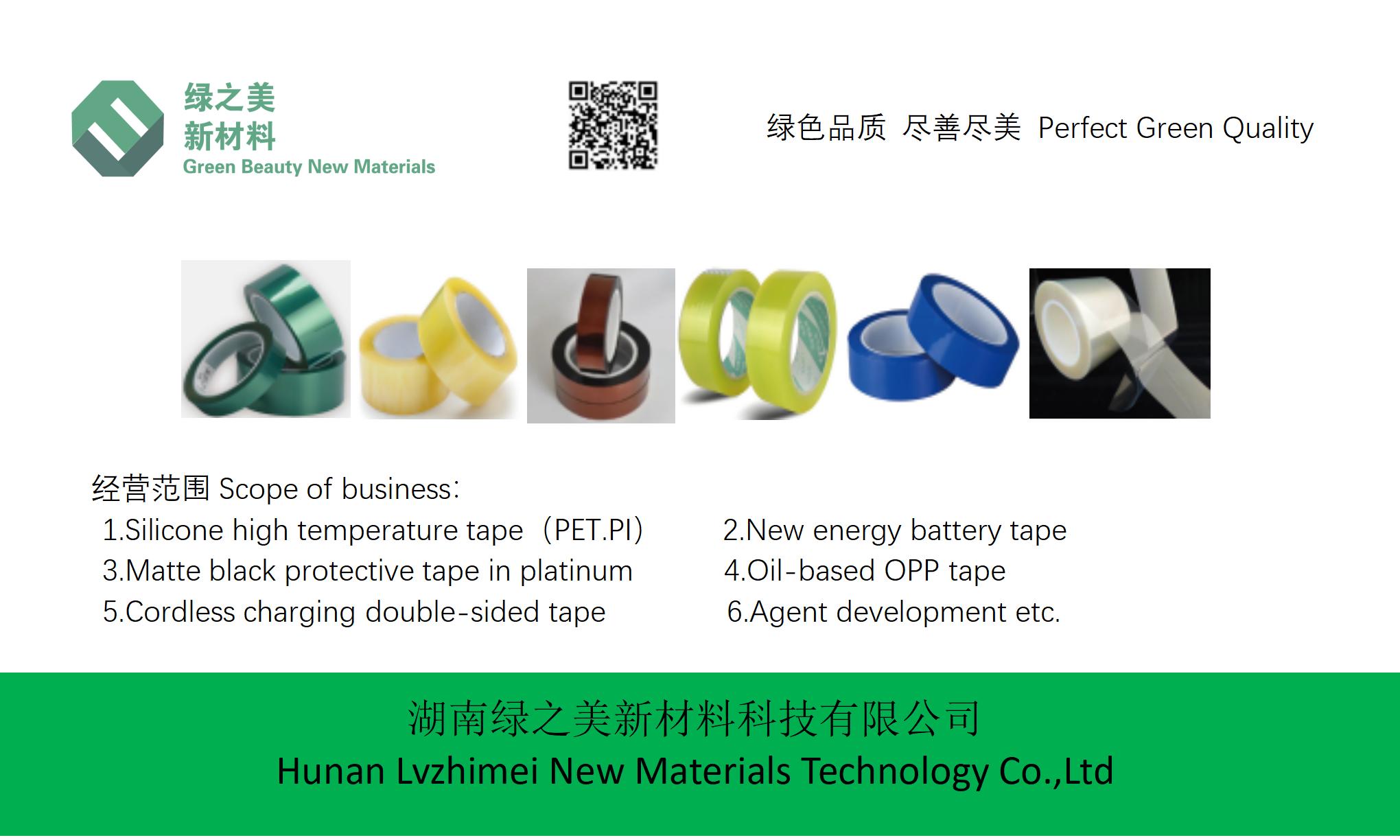