1. IntroductionPI tape, also known as Kapton tape, is a versatile adhesive tape made from polyimide film coated with high-temperature-resistant adhesive. Its exceptional properties, including thermal stability, electrical insulation, chemical resistance, and flexibility, make it indispensable in the electronics industry. From protecting circuit boards during soldering to insulating coils in transformers, PI tape plays a crucial role in ensuring the reliability and longevity of electronic components.
The demand for PI tape has surged with the advancement of technologies like 5G devices, electric vehicles, and miniaturized electronics, which often require components to withstand extreme temperatures and harsh environments. However, choosing the right PI tape can be challenging due to the diversity of available types, each designed for specific applications. This article aims to provide a comprehensive guide to help engineers, technicians, and manufacturers select the optimal PI tape based on their unique requirements.
2. Understanding Key Features
2.1 Adhesion: Types and ConsiderationsAdhesion is a critical factor in PI tape selection. The adhesive layer ensures the tape adheres firmly to surfaces, preventing displacement during processes like wave soldering or thermal cycling. Two main adhesive types dominate the market:
● Silicone-based Adhesive: Known for its high-temperature resistance (up to 300°C) and excellent flexibility, silicone adhesive is ideal for applications involving prolonged exposure to heat, such as reflow soldering. It offers strong initial tack but may require higher peel strength for permanent bonding.
● Acrylic-based Adhesive: Provides superior adhesion to a wide range of materials, including metals, plastics, and ceramics. Acrylic adhesive has lower temperature resistance (typically up to 200°C) but excels in long-term bonding and resistance to UV exposure. It is suitable for outdoor electronics or components subjected to sunlight.
Table 1: Adhesive Comparison
Feature | Silicone Adhesive | Acrylic Adhesive |
Temperature Range | Up to 300°C | Up to 200°C |
Initial Tack | Moderate | High |
Peel Strength | High (after curing) | Moderate to High |
UV Resistance | Limited | Excellent |
Long-term Bonding | Good | Superior |
Key Considerations:
● For wave soldering or reflow ovens, prioritize silicone adhesive to withstand thermal shock.
● For outdoor equipment or UV-exposed components, acrylic adhesive ensures durability.
● "Self-adhesive back blocking spray paint tape" variants offer dual functionality: adhesion for masking during painting and high-temperature resistance for subsequent processes.
2.2 Temperature Resistance: Grades and ApplicationsPI tape’s thermal stability is its defining feature. Different grades cater to specific temperature ranges:
● Standard Grade (≤260°C): Suitable for general electronics assembly, PCB protection, and over-soldering protection. Ideal for applications where intermittent heat exposure occurs (e.g., wave soldering).
● High-Temperature Grade (300°C+): Essential for environments with prolonged high temperatures, such as aerospace components, motor insulation, or 3D printer bed surfaces. These tapes often feature reinforced PI films and advanced adhesive formulations.
Table 2: Temperature Grades and Applications
Grade | Max. Temperature | Typical Applications |
Standard | 260°C | Circuit board masking, SMT processes |
High-Temp (300°C) | 300°C | Transformer coil insulation, automotive electronics |
Extreme-Temp (400°C+) | 400°C+ | Aerospace equipment, furnace insulation |
Key Considerations:
● Verify the continuous operating temperature rather than peak resistance to avoid premature degradation.
● For applications like battery cell manufacturing (e.g., lithium-ion tab fixation), ensure tape remains stable at temperatures ≥150°C during curing processes.
2.3 Electrical Insulation: Safety and PerformanceElectrical insulation is vital to prevent short circuits and arcing in high-voltage environments. PI tape’s performance is measured by:
● Dielectric Breakdown Voltage: The maximum voltage before insulation failure. High-grade PI tapes offer ≥4 kV/mm, suitable for transformers and power electronics.
● Volume Resistivity: Typically >1015 Ω·cm, ensuring minimal current leakage.
● Flame Retardancy: Most PI tapes meet UL 94 V-0 standards, reducing fire hazards.
Key Considerations:
● In high-voltage transformers or capacitors, choose tapes with certified dielectric strength.
● For medical devices or aerospace components, prioritize tapes with additional certifications (e.g., MIL-I-46058C).
3. Types of PI Tapes and Their Applications
3.1 Standard PI Tape vs. Specialized VariantsBeyond basic PI tape, manufacturers offer tailored variants:
● PI Tape with Conductive Layers: Incorporates metal coatings (e.g., copper or aluminum) for EMI/RFI shielding in telecommunications equipment.
● Anti-static PI Tape: Features surface resistivity of 106-109 Ω/sq, ideal for electrostatic-sensitive environments like semiconductor fabs.
● PI Tape with Release Liner: Allows precise die-cutting for自动化 applications without adhesive residue.
● PI Foil Tape: Combines PI film with metal foil for enhanced thermal conductivity and shielding.
3.2 Common Applications in Electronics Manufacturing
Application | Tape Requirements | Example Use Cases |
Circuit Board Protection | High-temp resistance, easy removal after soldering | Masking during wave/ reflow soldering |
Coil Insulation | Dielectric strength, mechanical durability | Transformers, high-voltage motors |
Battery Tab Fixation | Adhesion to metal, stability at 150°C+ | Lithium-ion cells, electric vehicle battery packs |
Thermal Interface Material | Thermal conductivity, flexibility | Heat sinks, LED modules |
PCB Gold Finger Protection | Anti-corrosion, low peel force | Preventing wear during connector insertion |
4. Choosing PI Tape: A Step-by-Step Guide
4.1 Assessing Environmental Conditions
● Temperature Range: Determine the maximum and continuous operating temperatures.
● Chemical Exposure: Identify if the tape will contact solvents, acids, or corrosive materials.
● Mechanical Stress: Evaluate if the tape will be subjected to bending, abrasion, or vibration.
4.2 Matching Tape Properties to Processes
● SMT Processes: Opt for tapes with high initial tack to stay in place during reflow ovens (e.g., PI material high-temp 300 tape).
● Spray Coating Masking: Select "back blocking spray paint tape" to prevent paint bleed-through while withstanding curing temperatures.
● High-Voltage Assemblies: Prioritize tapes with certified dielectric breakdown voltage (≥3 kV).
4.3 Budget and Long-term Cost ConsiderationsWhile high-grade PI tapes cost more upfront, they offer superior durability, reducing replacement frequency and costly downtime. Consider:
● Lifespan: Tapes with UV resistance or anti-aging properties延长使用寿命.
● Process Efficiency: Self-adhesive variants with liners save time during installation.
5. Additional Considerations: Compatibility and Handling
5.1 Surface Preparation and CleaningProper surface treatment (e.g., alcohol wiping to remove oils) enhances adhesion. Ensure compatibility with materials like copper, FR-4, or ceramics.
5.2 Storage and Shelf LifeStore PI tape in cool (≤30°C), dry environments to prevent adhesive degradation. Check expiration dates—most tapes retain performance for 1-2 years unopened.
5.3 Customization OptionsMany suppliers offer custom widths, lengths, or die-cut shapes for automation integration. Request samples for testing before bulk purchases.
6. Case Studies: Real-world Applications
6.1 PI Tape in SMT ProcessesIn surface mount technology (SMT), PI tape serves as a sacrificial mask during reflow soldering. A manufacturer producing LED boards faced tape delamination at 280°C, causing component damage. Switching to a high-temp silicone adhesive tape (rated 300°C) resolved the issue, reducing defects by 85% and saving $12,000/month in rework costs.
6.2 Battery Manufacturing and Lithium-ion CellsDuring lithium-ion battery assembly, PI tape fixes electrode tabs. A battery pack manufacturer transitioned from PET tape to PI tape with enhanced adhesion (peel strength 20 N/25 mm). This change improved tab retention during thermal cycling tests, boosting cell reliability and passing UL 1642 safety standards.
7. Market Trends and Future DevelopmentsThe PI tape market is evolving with:
● Nano-coatings: New formulations enhance adhesion without compromising thermal resistance.
● Smart Tapes: Embedded sensors track temperature or stress, enabling predictive maintenance in electronics.
● Sustainability: Eco-friendly PI tapes made from recycled polymers are gaining traction.
8. ConclusionSelecting the right PI tape requires a holistic assessment of application demands, environmental conditions, and process constraints. By prioritizing features like adhesion, temperature resistance, and electrical insulation, manufacturers can optimize performance, enhance reliability, and mitigate risks in electronics production. As technologies advance, staying abreast of emerging tape variants and testing protocols will ensure continued success in this dynamic field.
9. References
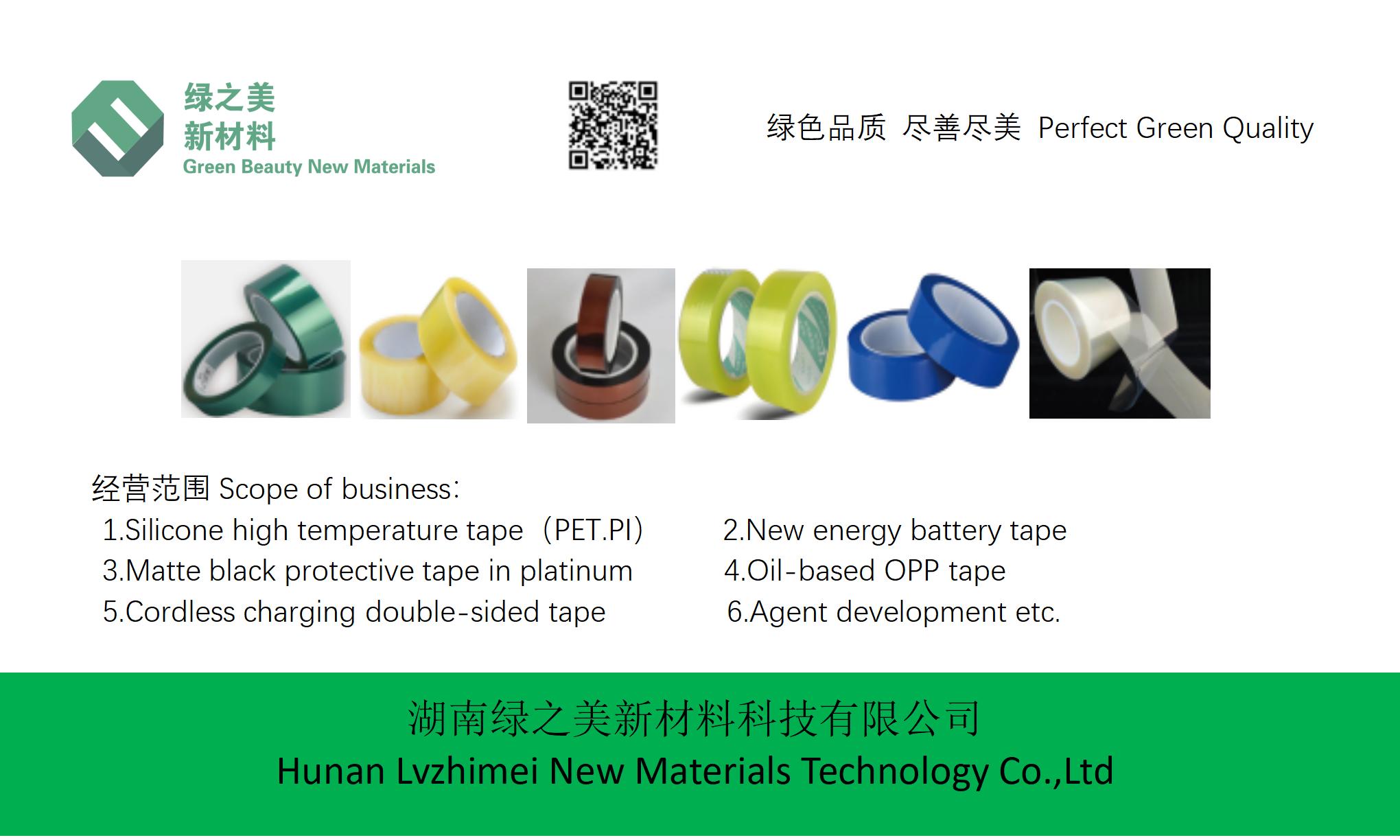
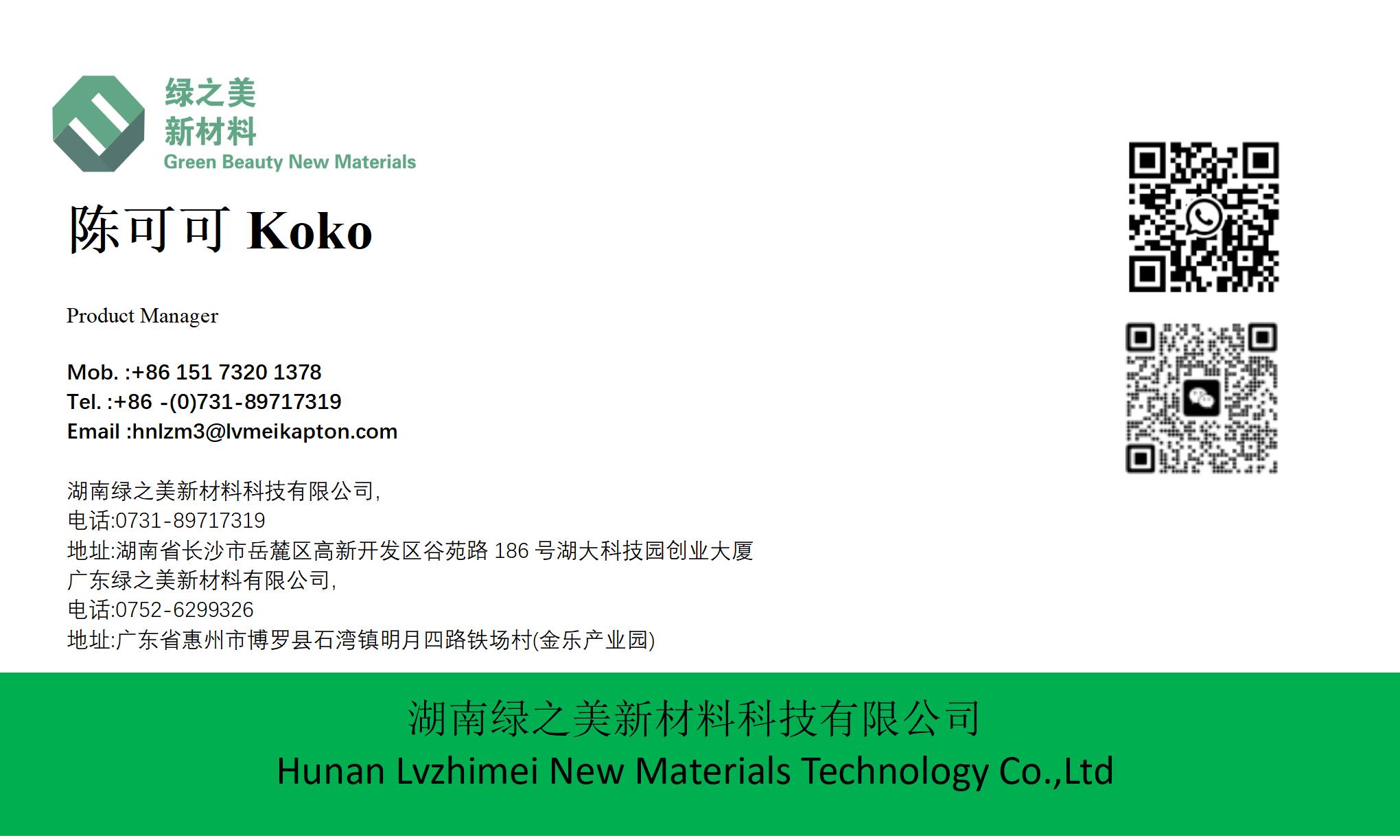