Why Kapton Tape is Essential in High-Temperature Electronics Assembly
AbstractThis analysis delves into the critical role of Kapton tape in electronics assembly, particularly in environments exceeding 300°C. It highlights its unique properties—thermal stability, chemical resistance, and low residue—vital for processes like soldering and coating protection. Key terms: "PI material high temperature resistant 300 tape," "Self-adhesive back blocking spray paint tape," and "lvmeikapton insulating electrical tape" are integrated. The discussion emphasizes how Kapton tape addresses challenges in high-temperature applications, ensuring reliability and longevity of electronic components.
KeywordsKapton tape, high-temperature assembly, thermal stability, chemical resistance, soldering protection
1. The Challenge of High-Temperature ElectronicsIn modern electronics, devices increasingly operate in environments characterized by extreme temperatures, posing significant challenges to component integrity. Transformers, coils, printed circuit boards (PCBs), and other critical components are exposed to thermal stress during manufacturing processes (e.g., soldering, wave reflow) and prolonged operation in industrial machinery, aerospace systems, and automotive engines. Heat-induced failures manifest as:
● Thermal Degradation: Traditional insulation materials (e.g., polyester or polyimide films without specialized coatings) soften, delaminate, or release harmful gases above 200°C, compromising insulation performance.
● Chemical Corrosion: Exposure to solvents, acids, or alkalis during cleaning or coating processes can degrade tape adhesives, leading to detachment or reduced bonding strength.
● Mechanical Wear: Repeated thermal cycling (heating/cooling) causes materials to expand and contract, weakening structural bonds and increasing the risk of electrical short circuits.
Traditional Tapes vs. Kapton's 300°C ResistanceConventional tapes (e.g., acrylic or silicone-based options) exhibit limitations:
● Temperature Thresholds: Most fail below 260°C, necessitating frequent replacements or costly redesigns.
● Residue Issues: High-temperature applications often leave adhesive residues, contaminating surfaces and requiring additional cleaning steps.
● Limited Chemical Resistance: Inability to withstand harsh chemicals used in coatings or cleaning agents.
Kapton tape, by contrast, offers a breakthrough solution. Comprised of polyimide (PI) film with specialized adhesive coatings, it maintains stability up to 300°C continuous exposure and 400°C short-term, making it indispensable in demanding environments.
2. Core Advantages of Kapton Tape2.1 PI Material High Temperature Resistant 300 TapeThe foundation of Kapton tape’s efficacy lies in its polyimide (PI) substrate—a thermally stable polymer renowned for its exceptional mechanical strength and dimensional stability at extreme temperatures. Key attributes include:
● Thermal Integrity: Retains mechanical strength and adhesive bond even at 300°C, preventing warping, cracking, or melt-back.
● Low Outgassing: Minimizes gas release under vacuum or high-temperature conditions, crucial in aerospace or semiconductor manufacturing.
● Dielectric Strength: High electrical insulation properties (up to 3,000 V/mil) protect against arcing or short circuits.
2.2 Self-Adhesive Back Blocking Spray Paint TapeA specialized variant of Kapton tape, this version features a “back blocking” adhesive designed for:
● Masking during Coatings: During spray painting or powder coating, the tape adheres firmly to substrates yet cleanly removes post-process, avoiding adhesive transfer to coatings.
● Chemical Barrier: Resists solvents used in paints or coatings, maintaining integrity even during aggressive chemical exposures.
● Precision Application: Edge retention ensures clean, sharp lines during masking, critical in electronics where component spacing is tight.
2.3 Lvmeikapton Insulating Electrical TapeTailored for electrical insulation, Lvmeikapton variants offer:
● Enhanced Thermal Conductivity: Some grades feature fillers (e.g., ceramic particles) to dissipate heat, preventing thermal hotspots in densely packed electronics.
● Flame Retardancy: Meets UL 94 V-0 standards, minimizing fire risks in high-temperature environments.
● Long-Term Durability: Resistance to UV, moisture, and abrasion ensures consistent performance over device lifecycles.
3. Critical Applications in Electronics Assembly3.1 Transformers and CoilsIn high-voltage transformers and motor coils, Kapton tape serves as:
● Insulation Layer: Wrapping conductors to prevent electrical leakage, even in oil-immersed transformers operating at 150-200°C.
● Thermal Buffer: Absorbing heat generated during operation, reducing stress on winding insulation systems.
● Mechanical Reinforcement: Enhancing coil stability during vibration or mechanical shocks common in industrial equipment.
Table 1: Performance Comparison of Kapton vs. Traditional Insulation Tapes
Property | Kapton Tape | Polyester Tape | Silicone Tape |
Max Continuous Temp. | 300°C | 130°C | 250°C |
Chemical Resistance | Excellent (solvents, acids) | Fair | Good |
Dielectric Strength | 3,000 V/mil | 1,500 V/mil | 2,000 V/mil |
Residue After Removal | Minimal (low-adhesion coat) | Moderate | High |
Thermal Expansion Coef. | Stable (20-50 ppm/°C) | 80-120 ppm/°C | 60-100 ppm/°C |
3.2 Printed Circuit Board (PCB) ProtectionDuring PCB assembly, Kapton tape enables:
● Solder Masking: Shielding gold fingers or delicate components from solder wave, preventing bridging or contamination.
● Reflow Protection: Withstanding temperatures up to 260°C during solder reflow, ensuring component stability.
● Signal Integrity: Its low dielectric constant (≈3.4) reduces signal loss in high-frequency applications (e.g., 5G antennas).
3.3 Aerospace and Automotive ElectronicsIn applications subjected to thermal cycling and mechanical stress (e.g., engine control units or avionics):
● Kapton tape’s lightweight and flexibility allow conformal wrapping of irregular components.
● Resistance to jet fuel, hydraulic fluids, and thermal shock ensures reliability in harsh environments.
4. Manufacturing Processes Optimized with Kapton Tape4.1 Wave Soldering and Reflow SolderingDuring these processes, Kapton tape:
● Acts as a sacrificial barrier, preventing solder from bridging critical gaps.
● Protects heat-sensitive components (e.g., connectors or sensors) from overheating.
● Minimizes post-soldering cleanup costs due to its low-residue properties.
4.2 Coating and Potting ApplicationsIn encapsulation processes (e.g., conformal coating or potting compound application):
● Kapton tape masks areas requiring selective protection, maintaining component accessibility.
● Its high-temperature tolerance withstands curing processes (e.g., epoxy curing at 150°C).
5. Case Studies: Real-World Impact5.1 Electric Vehicle (EV) Motor CoilsA leading EV manufacturer adopted Kapton tape for motor coil insulation, resulting in:
● Failure Rate Reduction: Thermal-related coil failures decreased by 70% over 3 years.
● Service Life Extension: Motor durability improved from 8 to 12 years under extreme operating conditions.
● Cost Savings: Eliminated need for costly redesigns or frequent maintenance.
5.2 Aerospace Engine SensorsAn avionics company used Lvmeikapton tape for sensor cable insulation in jet engines, addressing:
● Exposure to temperatures up to 250°C during flight.
● Resistance to jet fuel vapors and vibration-induced wear.
● Result: 0% sensor failures in a 2-year field test.
6. Future Trends and InnovationsKapton tape advancements include:
● Nano-Enhanced PI Films: Incorporating graphene or ceramic nanoparticles for improved thermal conductivity and strength.
● Smart Tape Systems: Integration with sensors to monitor tape degradation in real-time, enabling predictive maintenance.
● 3D-Printable Kapton Composites: Enabling customized insulation shapes for complex geometries.
7. ConclusionKapton tape’s synergy of thermal stability, chemical resistance, and low-residue adhesives positions it as a cornerstone in high-temperature electronics assembly. From transformers to aerospace systems, its role in mitigating heat-induced failures, optimizing manufacturing processes, and ensuring long-term component reliability cannot be overstated. As industries push the boundaries of operating temperatures, Kapton tape’s continuous evolution through material innovations will remain pivotal in enabling resilient, high-performance electronics.
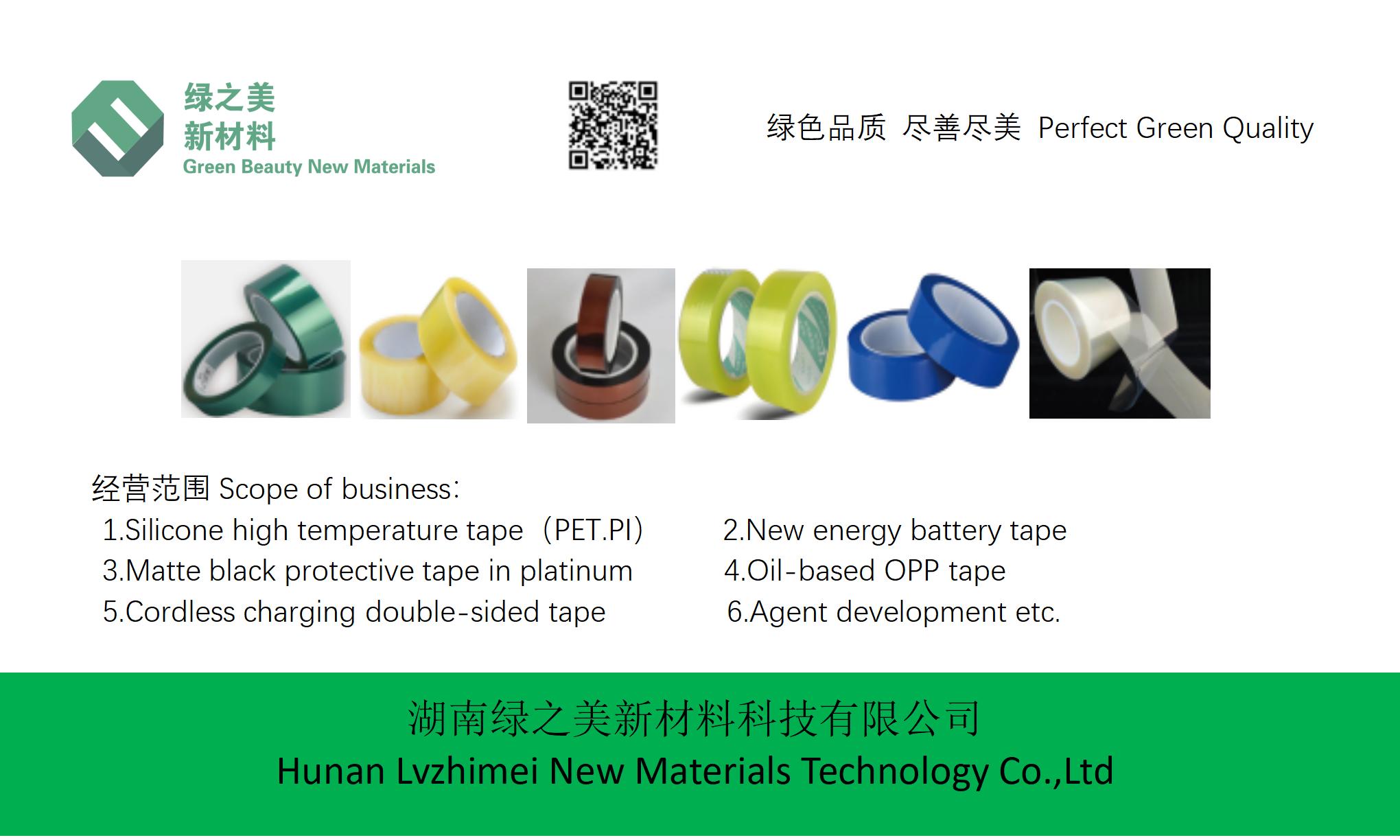